Cleanroom Safety – Stats & Facts
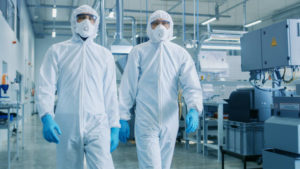
FACTS
The following are four basic factors that contribute to contamination through cleanroom technicians and/or operators:
- Hygiene: Small variations in personal hygiene can make a big difference when it comes to potential contamination within a highly controlled environment. If a person’s hands and/or face are not completely clean, there is a much higher number of potentially damaging particles seeping out from under protective clothing, including dandruff, hair and loose skin.
- Undergarments: While special protective garments do a lot to reduce contamination, the possibility can be reduced even further if operators pay attention to the types of street clothes they choose to wear to work. Fabrics like flannel, suede, velour and others that shed or form “pills” introduce extra risks into the environment. If they are not present in the first place, there is no possibility that these materials will escape from cleanroom garments and lead to contamination.
- Residual Smoke: Not quite the same as second hand smoke, residual smoke consists of particles that are left in the lungs and slowly emitted into the air after someone smokes a cigarette or cigar. If employees smoke during breaks or off-time, residual smoke can become a possible contaminant in even the most sterile of cleanrooms. Asking smokers to gargle or rinse their mouths will assist in diminishing this potential risk. The best solution, however, is to use facemasks which will prevent residual smoke, as well as other particles in exhaled breath, from entering the controlled environment.
- Operator Attitude: Not a physical factor, but just as important, is the attitude technicians and operators have as it relates to the probability of causing contamination at some point. Employees who don’t understand why they need to follow certain procedures, or just don’t care, are more likely to overlook necessary protocols and eventually cause something to go wrong.
STATS
- According to the National Environmental Balancing Bureau (NEBB), the number one cause of contamination within cleanrooms is the staff. In fact, cleanroom operators and technicians are responsible for 70% to 80% of cleanroom contamination problems.
- 6,000 fatal workplace injuries per year
- 50,000 deaths due to chemical exposures
- 6 million non-fatal injuries
- On average, pharmaceutical manufacturers spend approximately $3.1 million a year to remediate contamination events and occurrences. The charge for one alert, or interruption, can range from $1,000-$10,000 and the cost of a single action, or investigation, can be anywhere from $10,000 to $60,000.
- Recalls from product damage and contaminated pharmaceuticals can cost companies millions with more than 1,734 drug recalls reported by the U.S. Food and Drug Administration (FDA).