Combustible Dust – Stats and Facts
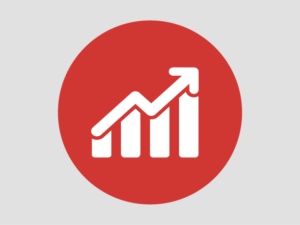
DID YOU KNOW?
Any combustible material can burn rapidly when in a finely divided form. If such a dust is suspended in air in the right concentration, under certain conditions, it can become explosible. Even materials that do not burn in larger pieces (such as aluminum or iron), given the proper conditions, can be explosible in dust form.
The force from such an explosion can cause employee deaths, injuries, and destruction of entire buildings. For example, 3 workers were killed in a 2010 titanium dust explosion in West Virginia, and 14 workers were killed in a 2008 sugar dust explosion in Georgia. The U.S. Chemical Safety and Hazard Investigation Board (CSB) identified 281 combustible dust incidents between 1980 and 2005 that led to the deaths of 119 workers, injured 718, and extensively damaged numerous industrial facilities.
A wide variety of materials that can be explosible in dust form exist in many industries. Examples of these materials include: food (e.g., candy, sugar, spice, starch, flour, feed), grain, tobacco, plastics, wood, paper, pulp, rubber, pesticides, pharmaceuticals, dyes, coal, metals (e.g., aluminum, chromium, iron, magnesium, and zinc). These materials are used in a wide range of industries and processes, such as agriculture, chemical manufacturing, pharmaceutical production, furniture, textiles, fossil fuel power generation, recycling operations, and metal working and processing which includes additive manufacturing and 3D printing.
Combustible dust accumulation is all too often an ignored hazard which if allowed unchecked accumulates in, and around your process machinery and vessels, settles on your floors, beams and all horizontal surfaces is a very real danger.
Combustible dust incidents have resulted in more than 342 fatalities worldwide last year alone, with an additional 441 injuries. There currently is no formal body collecting the data on combustible dust incidents, however they happen more often than most people realize. The US Chemical Safety Board identified 392 combustible dust incidents in the United States alone between 1980 and 2017, causing 185 fatalities and injuring 1,055 people.
Canada has not been immune to these incidents as well. In 2012 alone, multiple explosions caused the death of 4 workers and injured 41 more, but currently we have no system in place to record and report combustible dust incidents. There isn’t even a real way to track how many incidents are occurring, however they are happening with a frequency that can’t be ignored.
There are numerous laws across Canada which require you to address the combustible dusts in your facility. These include but aren’t limited to; the provincial Occupational Health and Safety Acts, the National and Provincial Fire codes, not to mention provincial requirements such as the ‘Pre-start safety and Health review’ (or PSR/PSHR) in Ontario, among others.
Failure to protect your facility and workers from combustible dust hazards can result in hefty fines, stop work orders and even criminal charges all across Canada. Large fines are increasingly common, and criminal charges usually follow fatalities. Just ask Veolia Sarnia, ON, who received $218,000 fine earlier this year when a combustible dust explosion claimed the life of an employee, not to mention the criminal charges laid against the manager, as well as the owner.
In existing facilities there is quite often a common misconception that the equipment and safety systems are adequate because of some sort of ‘grandfathering,’ however the grandfather clause doesn’t apply in virtually all circumstances, and ignorance of the hazard just doesn’t fly with authorities anymore. If you have dust in your facility and you can’t prove it isn’t combustible, then you are in a precarious position if you don’t have the proper safety systems in place.
The process to ensure your facilities are safe and compliant doesn’t have to be complicated. The first step is simple, determine if your dust(s) are in fact combustible (and if the dust is combustible how severe that combustion will be if ignition occurs). The proper test to determine this is the 20L Dust explosibility test which is performed to the dust testing standard.
In order to perform this test, you will be required to collect approximately 1 kg of the finest dust in your facility. The reason for this is the finest dust stays airborne the longest, accumulates on all horizontal surfaces and collects on the filter media of your air material separators among other equipment. Even if a great majority of the material you are handling in your facility is large particulate, the fines tend to accumulate and represent the actual hazard.
A good example of this can be illustrated with common granular sugar. When you pour sugar out of a larger bag into a serving container, a great majority of the sugar is granular and falls out of the bag and into the container, whereas the fines create a small dust cloud above the container floating around with the air currents. This fine dust in an industrial process will stay suspended, travel and accumulate. There are explosion protection process safety companies located in Canada that can provide this testing service as well as international testing experts in the U.S.
Combustible dust-fueled fires and explosions continue to injure and claim the lives of workers across a broad spectrum of industries, including the food, chemical, paper, pharmaceutical, and metal processing industries. In 2006, after investigating three combustible dust-related incidents over a two year period, the CSB conducted an in-depth study that identified 281 combustible dust incidents between 1980 and 2005 that killed 119 workers, injured 718, and extensively damaged industrial facilities. Since that time, the CSB has conducted four additional investigations into dust-related incidents, and the agency’s Office of Incident Screening and Selection continues to identify serious dust-related incidents on a regular basis.
The CSB believes that a general industry standard for combustible dust is greatly needed to prevent future tragedies. OSHA commenced rulemaking in October 2009; however, the agency has yet to issue a proposed rule. Moreover, the next step in the rulemaking process, the convening of a Small Business Regulatory Enforcement Fairness Act (SBREFA) panel, has been postponed several times.
For a dust explosion to occur, everything has to be lined up just right. Unlike a fire, which can be started by a trio of elements — fuel, an ignition source and oxygen — a dust explosion can occur only if a pentagon comprising two additional elements, dispersion and confinement, come together.
That destructive constellation is now being investigated as a possible cause behind the explosion of two sawmills in British Columbia that blew up months apart from each other. On January 20, 2012, an explosion and fire destroyed Babine Forest Products mill in Burns Lake, killing two workers and seriously injuring more than a dozen. On April 23, an explosion and the resulting fire razed Lakeland Mills in Prince George, claiming two employees and injuring 22.
The similarities between the two explosions are striking — both are sawmills, dust was present in both facilities and both are working with beetle-infested wood. A similarity so uncanny that it prompted a review, an industry-wide directive order and several investigations to find out just what went wrong, and how it could go so wrong.
The destruction of the two sawmills has triggered a search for answers that will be close to the heart of many industries that generate fine particles — from mills that process wood, grain and sugar; chemical manufacturing plants and facilities that fabricate rubber and plastic products; to coal-fired power plants.
On April 25, provincial labour minister Margaret MacDiarmid convened an urgent meeting involving representatives from the industry, United Steelworkers and WorkSafeBC to review mill safety and compile a document on industry best practices relating to combustible dust control in sawmills.
The following day, the provincial safety regulator issued a directive order to all sawmill operators to conduct a full hazard identification, risk assessment and safety review with particular focus on combustible dust, dust accumulation and potential ignition sources. “WorkSafeBC officers will be following up on these orders to confirm the ordered actions have been taken and sawmills are in compliance with the Workers Compensation Act and Occupational Health and Safety Regulation in regard to combustible dust and potential safety hazards,” a WorkSafeBC statement noted in April.
Until the investigation has concluded, Roberta Ellis, vice-president of corporate services with WorkSafeBC in Richmond, British Columbia, says it “cannot speculate, based on the similarities, as to the cause of these events.”
It did, however, reveal in a statement in May the ignition sources in both investigations appear to have been located at the conveyor belt level where electrical and/or mechanical equipment was in operation in areas contained by walls and equipment. These areas are located at the basement or lower level of both mills.
Officers inspecting all sawmills and associated site facilities under the directive order “will be paying particular, but not exclusive, attention to areas similar to those identified in the Babine Forest Products and Lakeland Mills investigations,” the statement notes.
The Council of Forest Industries in Vancouver has also established a task force comprising representatives and stakeholders from the wood products manufacturing industry to investigate combustion risks in mills. The task force, which reports to a CEO Action Committee, “is a significant collaborative effort to ensure that British Columbia’s wood products manufacturers are operating to the absolute highest standards,” Hank Ketcham, chief executive officer of West Fraser, says in a statement.
Don Kayne, chief executive officer of Canfor, adds that “we have taken every opportunity to increase our efforts in safety since the serious incidents at Lakeland and Babine, and this joint initiative is a next and very important step.”
Stephen Hunt, director of western Canada (district 3) with the United Steelworkers, went to Babine Forest Products mill with several union representatives following the incident. “Nobody from anywhere could recall a catastrophic explosion in a sawmill that literally blew the mill right off the face of the earth,” he says. When the mill in Burns Lake exploded, “I think it is safe to say that everybody is convinced that it was a one-off; something happened in that mill that was so unique that they could not be replicated,” Hunt continues. “Then three months later, we blow another one up.”
Fact Check
The two incidents have raised many questions on why dust particles are hazardous and what makes them combustible.
Combustible dust — also known as dry, deflagarable dust — is a wood particulate with an average diameter of 420 micrometers or smaller and has a moisture content of less than 25 percent, notes information from WorkSafeBC. “The drier the dust, the finer it can become and it is more of a fire explosion hazard,” says John Astad, director of the Combustible Dust Policy Institute in Santa Fe, Texas.
Combustible dusts are often organic or metal dusts that are finely ground into very small particles. Types of dusts include, but are not limited to metal dust (such as aluminum and magnesium); wood dust; plastic dust; biosolids; organic dust (like sugar, paper, soap and dried blood); and dusts from certain textiles, notes information from EMSL Canada, Inc. in Mississauga, Ontario. The United States-based firm is one of two companies identified by WorkSafeBC as being able to perform combustible dust testing.
Suspended dust burns more rapidly while confinement allows for pressure to build up. The initial explosion can cause dust that has settled over the years to become airborne, resulting in a secondary explosion that propagates throughout the plant, often with disastrous results.
Apart from primary and secondary explosions, there is also a “multitude of non-consequential combustible-related fires,” Astad notes. While the majority of combustible dust-related incidents do not result in injuries, fatalities or property loss, “these can be precursors to catastrophic events.”
Weakest Link
No amount of dust, it seems, is too little to be ignored. Any surface that has more than five per cent of dust accumulation on it has to be cleaned off. In fact, a thickness that exceeds an eighth of an inch is too much, says Craig Kennedy, owner of Kennedy Forest and Safety Consultants in Williams Lake, British Columbia. “That is the thickness of two nickels.”
Potentially explosive particles can accumulate wherever dust is generated, says Dr. Graeme Norval, PhD, associate chair and undergraduate coordinator with the department of chemical engineering and applied chemistry at the University of Toronto. For sawmills, this means places where the blades are located and where lumber gets transported. In sugar mills, vulnerable spaces include those where grinding operations, transportation of materials on conveyor belts and bagging of sugar and flour take place.
In other words, “anytime you are changing a particle size, that is when you have a vulnerability,” Astad notes.
Many new, automated mills are using more efficient, computerized technology to process wood, generating finer dust in greater amounts which, when suspended, presents an explosion risk, Kennedy explains. “They are pounding wood through really fast,” he adds, citing bandsaws, fast-moving table saws and circular saws as examples.
Hunt agrees. “We are finding that, like in many workplaces, the size and speed of the saw blades have changed; the nature of the dust coming off has changed.” These changes demands the accompaniment of safety controls, although “it appears that that may have been left behind,” Hunt suggests.
Transfer points like conveyor belts, bucket elevators, mixers and dryers are vulnerable to the risk of dust explosion. Friction from moving equipment — like a bucket elevator with its metal rubbing against a casing — and industrial-powered equipment, such as forklifts, can also cause fires or explosion when hot surfaces from motors, brakes and engine exhaust system meet suspended dust in sufficient amounts. “All that is missing is an ignition source,” Astad says, noting that explosion-proof forklifts should be used to ensure safe operation in environments where dust is being generated.
Any activity that involves heat, electricity and an open flame can serve as an ignition source. A worker doing hot work on the other side of a process equipment, Astad cites by way of example, can accumulate sufficient electrostatic charge to potentially ignite dust accumulation in that area. The possibility of an electric rotor or electrical panel arcing or sparking presents an additional risk.
KEEP IN MIND
Combustible dusts are fine particles that present an explosion hazard when suspended in air in certain conditions. A dust explosion can be catastrophic and cause employee deaths, injuries, and destruction of entire buildings. In many combustible dust accidents, employers and employees were unaware that a hazard even existed. It is important to determine if your company has this hazard, and if you do, you must take action now to prevent tragic consequences.
How Dust Explosions Occur
In addition to the familiar fire triangle of oxygen, heat, and fuel (the dust), dispersion of dust particles in sufficient quantity and concentration can cause rapid combustion known as a deflagration. If the event is confined by an enclosure such as a building, room, vessel, or process equipment, the resulting pressure rise may cause an explosion. These five factors (oxygen, heat, fuel, dispersion, and confinement) are known as the “Dust Explosion Pentagon”. If one element of the pentagon is missing, an explosion cannot occur.
Catastrophic Secondary Explosions
An initial (primary) explosion in processing equipment or in an area where fugitive dust has accumulated may dislodge more accumulated dust into the air, or damage a containment system (such as a duct, vessel, or collector). As a result, if ignited, the additional dust dispersed into the air may cause one or more secondary explosions. These can be far more destructive than a primary explosion due to the increased quantity and concentration of dispersed combustible dust. Many deaths in past accidents, as well as other damage, have been caused by secondary explosions.
Industries at Risk
Combustible dust explosion hazards exist in a variety of industries, including: agriculture, chemicals, food (e.g., candy, sugar, spice, starch, flour, feed), grain, fertilizer, tobacco, plastics, wood, forest, paper, pulp, rubber, furniture, textiles, pesticides, pharmaceuticals, tire and rubber manufacturing, dyes, coal, metal processing (e.g., aluminum, chromium, iron, magnesium, and zinc), recycling operations, and fossil fuel power generation (coal).
Prevention of Dust Explosions
To identify factors that may contribute to a explosion, OSHA recommends a thorough hazard assessment of:
- All materials handled;
- All operations conducted, including byproducts;
- All spaces (including hidden ones); and
- All potential ignition sources.
Dust Control Recommendations
- Implement a hazardous dust inspection, testing, housekeeping, and control program;
- Use proper dust collection systems and filters;
- Minimize the escape of dust from process equipment or ventilation systems;
- Use surfaces that minimize dust accumulation and facilitate cleaning;
- Provide access to all hidden areas to permit inspection;
- Inspect for dust residues in open and hidden areas at regular intervals;
- If ignition sources are present, use cleaning methods that do not generate dust clouds;
- Use only vacuum cleaners approved for dust collection; and
- Locate relief valves away from dust deposits.
Ignition Control Recommendations
- Use appropriate electrical equipment and wiring methods;
- Control static electricity, including bonding of equipment to ground;
- Control smoking, open flames, and sparks;
- Control mechanical sparks and friction;
- Use separator devices to remove foreign materials capable of igniting combustibles from process materials;
- Separate heated surfaces from dusts;
- Separate heating systems from dusts;
- Select and use industrial trucks properly;
- Use cartridge activated tools properly; and
- Use an equipment preventive maintenance program.
Injury and Damage Control Methods
- Separation of the hazard (isolate with distance);
- Segregation of the hazard (isolate with a barrier);
- Deflagration isolation/venting;
- Pressure relief venting for equipment;
- Direct vents away from work areas;
- Specialized fire suppression systems;
- Explosion protection systems;
- Spark/ember detection for suppression activation;
- Develop an emergency action plan; and
- Maintain emergency exit routes.
Essentially, a combustible dust is any fine material that has the ability to catch fire and explode when mixed with air. Combustible dusts can be from:
- most solid organic materials (such as sugar, flour, grain, wood, etc.)
- many metals, and
- some nonmetallic inorganic materials.
Some of these materials are not “normally” combustible, but they can burn or explode if the particles are the right size and in the right concentration.
Therefore, any activity that creates dust should be investigated to see if there is a risk of that dust being combustible. Dust can collect on surfaces such as rafters, roofs, suspended ceilings, ducts, crevices, dust collectors, and other equipment. When the dust is disturbed and under certain circumstances, there is the potential for a serious explosion to occur. The build-up of even a very small amount of dust can cause serious damage.
Technical Definition of Combustible Dust
The technical definitions for combustible dust vary. In Canada, the Hazardous Products Regulation (WHMIS 2015) defines combustible dust as ” a mixture or substance that is in the form of finely divided solid particles that, upon ignition, is liable to catch fire or explode when dispersed in air”.
Another example is Alberta’s Occupational Health and Safety Code which defines combustible dust as “a dust that can create an explosive atmosphere when it is suspended in air in ignitable concentrations”.
The Occupational Safety and Health Administration (OSHA) in the United States defines combustible dust as “a solid material composed of distinct particles or pieces, regardless of size, shape, or chemical composition, which presents a fire or deflagration hazard when suspended in air or some other oxidizing medium over a range of concentrations”.
Examples of Materials That Can Be A Combustible Dust Hazard
Many materials can become combustible under specific situations. Examples include:
- agricultural products such as egg whites, powdered milk, cornstarch, sugar, flour, grain, potato, rice, etc.
- metals such as aluminum, bronze, magnesium, zinc, etc.
- chemical dusts such as coal, sulphur, etc.
- pharmaceuticals
- pesticides
- rubber
- wood
- textiles
- plastics
There are many, many more types of materials that may become a combustible dust. The US OSHA has created a poster which lists more examples.
What workplaces are at risk for a dust explosion?
Dust explosions have occurred in many different types of workplaces and industries, including:
- Grain elevators,
- Food production,
- Chemical manufacturing (e.g. , rubber, plastics, pharmaceuticals),
- Woodworking facilities,
- Metal processing (e.g. , zinc, magnesium, aluminum, iron),
- Recycling facilities (e.g. , paper, plastics, metals), and
- Coal-fired power plants.
Dusts are created when materials are transported, handled, processed, polished, ground and shaped. Dusts are also created by abrasive blasting, cutting, crushing, mixing, sifting or screening dry materials. The buildup of dried residue from the processing of wet materials can also generate dusts. Essentially, any workplace that generates dust is potentially at risk.
How do combustible dust explosions happen?
Any fire needs three elements. These elements are known as the “fire triangle”:
- Fuel to burn
- Oxygen Ignition source (heat, spark, etc. )
- A dust explosion needs two additional elements – known as the “dust pentagon”:
- Dispersion of dust particles in the right concentration, and
- Confinement of the dust cloud.
Dispersion means the dust particles are suspended in air. Confinement means the dust is in an enclosed or limited space. This restriction allows pressure to build up, increasing the likelihood of an explosion.
What is deflagration?
Deflagration is a term often used to describe combustible dust explosions. A deflagration is an “ordinary” fire such as a gas stove, burning wood or paper, and even the burning of gasoline vapour inside the cylinder of an automobile. In a deflagration, a burning substance releases heat, hot gases, and energetic particles or sparks that ignite and spread the fire.
In a dust explosion, the deflagration processes happen so rapidly that the heated air and gaseous fire products (such as carbon dioxide) produce extreme air pressure that can blow out walls and destroy structures.
What are primary and secondary dust explosions?
When combustible dusts ignite, there are often two explosions known as primary and secondary explosions.
The primary dust explosion is the first explosion. It occurs when there is a dust suspension in a confined space (such as a container, room, or piece of equipment) that is ignited and explodes.
The primary explosion will shake other dust that has accumulated. When this dust becomes airborne, it also ignites. This secondary dust explosion is often more destructive than the primary one.
What conditions are needed for a dust explosion to happen?
The basic requirements for a dust explosion to occur is that combustible dusts are suspended in air and are ignited. In practice, for a dust explosion to occur, a number of conditions must be met including:
- The dust must be combustible and release enough heat when it burns to sustain the fire.
- The dust must be capable of being suspended in air.
- The dust must have a particle size capable of spreading the flame.
- The concentration of the dust suspension must be within the explosible range.
- An ignition source must be in contact with the dust suspension.
- The atmosphere must contain sufficient oxygen to support and sustain combustion.
- There is a form of confinement or enclosure that allows pressure to build.
How do I identify a combustible dust hazard?
There are many variables that must be considered – the particle size of the dust, the method of dispersion, ventilation system characteristics, air currents, ignition sources, confinement of the dust cloud, physical barriers, and so on. As a result, the often quoted “rule of thumb” about dust accumulation (such as being able to write in the dust, or the dust being the thickness of a paperclip, dime or quarter, or the amount of visibility through a dust cloud) is not always reliable.
Best practice is to keep the workplace as dust free as possible.
Conduct a risk assessment and look specifically for dust explosion possibilities. Below are some questions that may help.
Processes
- Do you manufacture or use any materials (and their by-products) that can become a dust?
- Do you have processes such as abrasive blasting, cutting, grinding, sieving, polishing, cleaning, or other tasks that create dust?
Ignition sources
- Do you have ignition sources (e.g. , sparks, fire/flames, stoves, kilns, or welding flames)?
- Can dust enter or accumulate on electrical enclosures or equipment?
- Does your workplace have a no-smoking policy? Are there measures to isolate smoking and ignition sources away from production areas?
Housekeeping
- Do you know if there are open areas and overhead structures where dusts may accumulate?
- Have you looked for “hidden” areas where dust may accumulate (e.g. , behind false ceilings, inside ventilation or conveyor equipment, in ducts, on support beams, etc. )?
- Do you have a housekeeping program to regularly remove dust?
- Do you have a dust collection system in place?
- If yes, does your dust collection system conform to local requirements (e.g. , fire code)?
Education and training
- Are employees aware of combustible dust and its hazards?
- Do employees follow housekeeping rules and take steps to reduce dust and remove ignition sources?
- Have employees been trained and educated on safe methods for cleaning?
Prevention Measures
Once you have identified the hazards, you need to take prevention measures.
Eliminate
- Where possible, avoid horizontal surfaces (such as window ledges, beams, light fittings, etc. ) where dust can accumulate.
- Eliminate “hidden” areas where dust can accumulate unnoticed.
- Do not use brooms or compressed air hoses to clean surfaces. Only use vacuums approved for dust collection.
- Only use a dust collection / dust extraction system that is designed to eliminate or control combustible dust. Using most models of fans typically stirs the dust, adding dust particles into the air and worsening the situation.
Substitute
Install smooth ceilings and other surfaces (instead of a rough finish) to minimize dust accumulation and to make cleaning easier.
Engineering
- Use an appropriate dust extraction and collection system with the inlet located as close to the dust producing process as possible. Follow required standards and codes when installing these systems. Locate dust collectors outdoors, where possible.
- Direct explosion venting away from areas where there may be employees.
- Use appropriate electrical and ventilation equipment.
- Keep all mechanical and electrical equipment in good repair.
- Keep static electricity under control, which includes the bonding and grounding of equipment. Check all bonded and grounded equipment regularly to ensure the bonds are in good condition.
- Check equipment that may wear (e.g. , bearings) as they may generate heat and become an ignition source.
- Remove open flames, sparks, friction, heat sources, and other sources of ignition.
- Select and use intrinsically safe tools or machinery.
- Put covers around pipes and cables, or embed pipes and cables in the walls, where possible, to reduce surfaces where dust can accumulate.
Administration
- Develop and implement a combustible dust inspection and control program which outlines how often inspections will occur and how dust will be controlled.
- Develop a hot work permit system for activities such as welding and cutting.
- Develop an ignition control program to eliminate or reduce sources of ignition. Keep ignition sources away from dusty areas or use suitable controls.
- Educate all employees about combustible dusts, the hazards, and how they can help eliminate the risk of fire and explosions.
- Inspect for dust at regular intervals.
- Establish a housekeeping program that will remove dust regularly.
- Use proper equipment and techniques when cleaning dust. Care must be taken to minimize dust clouds, and only use vacuums approved for dust collection.
- Regularly inspect machines, ducts, and ventilation systems for dust. Repair or clean promptly.