Dealing With Hazards Meeting Kit
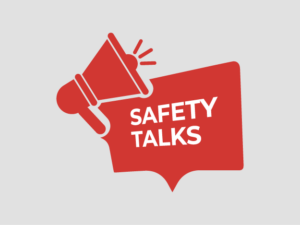
DEALING WITH HAZARDS SAFETY TALK
We face hazards everyday whether walking out of our house or doing tasks at work. Employees need the training and knowledge to recognize hazards and take action to mitigate them.
PROBLEM OF WORKPLACE HAZARDS
But often this is what happens. Hazards are identified but no action follows to eliminate the hazard. When this occurs, the hazard is left to be dealt with you anyone in that work area.
EXAMPLES OF HAZARDS BEING LEFT TO BE DEALT WITH
- A piece of metal is sticking up out of the ground in a work area on a construction site. An employee lets his fellow workers know of the presence of the metal however that is all the action that is taken. Anyone walking through that area still has to deal with that hazard. A more effective response would be to call a piece of heavy equipment over to remove the metal from the ground.
- A leaky pipe is causing a wet spot on a factory floor. The leak was spotted months ago, but the only response was to put a sign up warning personnel of slick conditions. Taking the time to fix the pipe properly ensures employees do not slip on the wet conditions.
SAFETY HAZARD ASSESMENT PROTECTION
Workers cannot be properly protected against hazards that they are unaware of or unprepared to deal with those hazards. Avoid those “blind spots” by a thorough safety hazard assessment.
SIX TYPES OF WORKPLACE HAZARDS
- Safety hazards
Safety hazards is number one on the list of 6 types of workplace hazards. These hazards play an affect on employees who work directly with machinery or in construction sites.
- Biological hazards
The definition of biological hazards, commonly known as biohazards, can be any biological substance that could cause harm to humans. Biological hazards exposure to harm or disease from working with animals, people, or infectious plant materials.
- Physical hazards
Physical hazards might the least obvious. Physical hazards affect workers in extreme weather conditions or harmful working environments. Physical hazards can be any factors within the environment that can harm the body without necessarily touching it.
- Ergonomic hazards
Ergonomic safety hazards occur when the type of work, body positions, and working conditions put a strain on your body. They are the hardest to spot since you don’t always immediately notice the strain on your body or the harm that these hazards pose.
- Chemical hazards
Chemical hazards are present when a worker is exposed to any chemical preparation in the workplace in any form (solid, liquid or gas).
- Work organization hazards
Safety hazards or stressors that cause stress (short-term effects) and strain (long-term effects). These are hazards associated with workplace issues such as workload, lack of control and/or respect, workplace violence, etc.
COMMON HEALTH RISKS
Common health risks associated with workplace hazards include: breathing problems, skin irritation, damage to muscles, bones and joints, hearing damage, reduced wellbeing.
PREVENT WORKPLACE HAZARDS
The best way to protect yourself and your employees from workplace hazards is to identify and manage them and take reasonable steps to prevent their potential to harm.
In order to control workplace hazards and eliminate or reduce the risk, you should take the following steps:
- identify the hazard by carrying out a workplace risk assessment;
- determine how employees might be at risk;
- evaluate the risks;
- record and review hazards at least annually, or earlier if something changes.
FINAL WORD
Do not just “deal” with hazards, eliminate them whenever possible. All too often the time or energy is not spent to properly address hazards to make a work area or work task safe. It is true that taking some action is better than none at all, but often it does not take much more time to get the problem fully corrected and addressed to be sure no one will be injured by that hazard.