Emergency Equipment – Stats and Facts
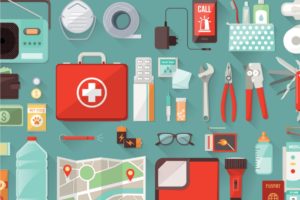
DID YOU KNOW?
We’ve all read the statistic that tells us about 2,000 workers in the United States suffer eye injuries requiring medical treatment every day. It’s usually attributed to NIOSH and followed or preceded by the admonition that at least 90 percent of those injuries were preventable through the use of the proper PPE and also emergency eyewash and shower equipment.
Safety PPE prevents hazardous exposures when used and maintained correctly. Workers in occupations where it is commonly used are quite familiar with it—their hard hat, high-visibility and/or protective apparel, fall harness, cut-resistant gloves, safety footwear, etc.—and appreciate why its use is required on the job. But eyewash and shower equipment is different, in that, like fire sprinklers and fire alarms, it’s rarely needed in an actual emergency situation. Fire sprinklers and fire alarms and share another similarity with emergency eyewash and shower equipment: You have to test it regularly to ensure it will function as needed when a real emergency happens.
Workplaces where employees may be exposed to harmful corrosive materials should be equipped with eyewash and shower units that are inspected annually to ensure they comply with the ANSI/ISEA Z358.1-2014 standard. These employers should activate these units weekly in order to make certain it is operational and to get rid of any sediment that may be in the supply line. This testing should continue as long as necessary to ensure there is flushing fluid supply at the device’s delivery head and to clear sediment.
Placement of the emergency equipment is very important. Manufacturers say that it’s key to have an appropriate flushing system located on the same level and within 10 seconds’ travel distance, or about 55 feet, from the hazard; to protect the equipment and supplies against extremely hot or cold temperatures; and to get rid of any and all trip hazards between the hazard and the equipment. (In other words, a person in pain and with possibly obstructed vision should be able to traverse the path from hazard to the flushing units within seconds.)
Eye injury statistics are available from a variety of sources, including the American Optometric Association, the American Academy of Ophthalmology, NIOSH, the National Safety Council, and others. The National Safety Council’s Injury Facts, 2016 Edition tells us there were 22,120 occupational eye injuries in the U.S. private sector during 2013, and these injuries accounted for 2.4 percent of the private-sector injuries that year resulting in days away from work. Injuries affecting the back, hand, head, and knees caused larger percentages of the lost-time cases that year, but eye injuries are especially costly and debilitating.
OSHA has stated that thousands of workers are blinded each year from work-related eye injuries that could have been prevented, and the agency reported that eye injuries alone cost more than $300 million per year in lost production time, medical expenses, and workers’ compensation.
Still, it’s worth pointing out here that more injuries occur at home than anywhere else, according to CDC’s National Center for Health Statistics. We need to be wearing protective eyewear and avoiding vision hazards during activities at home just as we do in the workplace.
Potential eye hazards on the job include:
- Dust, concrete, metal, and particles
- Chemical splashes and fumes
- Radiation (especially visible light, ultraviolet radiation, heat or infrared radiation, and lasers)
- Bloodborne pathogens in health care from blood and body fluids
Some workers face multiple eye hazards, such as heat and particles simultaneously; conduct a hazard assessment before selecting eye protection for all types of hazardous exposures.
After an injured worker has used an eyewash or emergency shower unit for the specified 15-minute period, the individual should visit a doctor to determine whether anything more needs to be done for the preservation of his or her vision, the American Optometric Association advises.
More than 50,000 U.S. workers die each year due to occupational injuries and illnesses, according to Preventable Deaths 2014, a report released by the National Council on Occupational Safety and Health (National COSH).
“No one should have to risk their life simply to earn a living,” said Jessica Martinez, deputy director of National COSH. “Many of the injuries and illnesses that are killing American workers can be prevented. We know the safety systems, equipment and training that can stop people from dying on the job, and it’s absolutely urgent that we take action to protect workers and their families.”
Key findings of Preventable Deaths 2014 include:
- In 2012, at least 4,383 workers died from sudden traumatic injuries in 2012 – a preliminary figure that is likely to increase when final data are released by the U.S. Bureau of Labor Statistics at the end of April.
- Tens of thousands of workers die each year from long-term occupational illnesses. One estimate puts the toll at 53,000 deaths annually, causing untold harm and suffering – and costing the U.S. economy $45.5 billion a year.
- Nearly 700 deaths can be prevented every year by timely adoption of a standard limiting workplace exposure to silica. This silent killer can cause silicosis, lung disease, cancer and other fatal conditions.
The report highlights data showing high risks in the workplace faced by Hispanic workers. For each of the past five years, the on-the-job fatality rate for Latino workers has been significantly higher than for U.S. workers as a whole.
Preventable Deaths 2014 also identifies proven approaches to prevention for each of the six major causes of occupational fatalities identified by the Bureau of Labor Statistics: transportation incidents, contacts with objects and equipment, falls to a lower level, workplace violence, exposure to harmful substances and environments, and fires and explosions.
The report also details actions taken by local health and safety coalitions to advocate for safer workplaces and to prevent workplace fatalities. Local organizations in California, Massachusetts, New York, Tennessee, Texas and Wyoming this week are issuing reports on workplace fatalities in their individual states in conjunction with Workers’ Memorial Week activities.
Workers’ Memorial Day Honors Workers
“Today, we honor the dead and fight for the living,” said Jessica Martinez, deputy director of the National Council for Occupational Safety and Health. “We know that many of the injuries and illnesses that are killing American workers can be prevented. Employers must be held accountable when they fail to observe well-established well-established safety practices. And workers must have the education, training, resources and protection against retaliation they need to stand up for workplace safety.”
Several groups are releasing reports about workplace injuries, illnesses and fatalities. These groups include:
California: WORKSAFE, “Dying at Work in California: The Hidden Stories Behind the Numbers.” Details the stories of temporary workers, transit workers and food processing workers. Outlines the industries with highest rate of fatalities, profiles the cost of workplace injuries and illnesses, and summarizes steps health and safety agencies need to take to prevent workplace injuries and fatalities.
Massachusetts: MASSCOSH, Dying for Work in Massachusetts: Loss of Life and Limb in Massachusetts Workplaces.” Details, background and recommendations on the 48 Massachusetts workers who died on the job; the estimated 480 who died from occupational diseases; the estimated 1,800 who were newly diagnosed with cancers caused by workplace exposure and the 50,000 more who were seriously injured at work.
KEEP IN MIND
Your employees may need personal protective equipment to evacuate during an emergency. Personal protective equipment must be based on the potential hazards in the workplace. Assess your workplace to determine potential hazards and the appropriate controls and protective equipment for those hazards. Personal protective equipment may include items such as the following:
- Safety glasses, goggles, or face shields for eye protection;
- Hard hats and safety shoes for head and foot protection;
- Proper respirators;
- Chemical suits, gloves, hoods, and boots for body protection from chemicals;
- Special body protection for abnormal environmental conditions such as extreme temperatures; and
- Any other special equipment or warning devices necessary for hazards unique to your worksite.
How do you choose appropriate respirators and other equipment?
Consult with health and safety professionals before making any purchases. Respirators selected should be appropriate to the hazards in your workplace, meet OSHA standards criteria, and be certified by the National Institute for Occupational Safety and Health.
Respiratory protection may be necessary if your employees must pass through toxic atmospheres of dust, mists, gases, or vapors, or through oxygen-deficient areas while evacuating. There are four basic categories of respirators for use in different conditions.
The Occupational Safety & Health Administration (OSHA) mandates certain industries must have specific items in their first aid kit. But for most offices, a first aid kit won’t be enough in the event of a fire, tornado, or other threat. Do you know the location of the emergency equipment in your office? These items should be placed in an area where the whole team can access it immediately in the event of a crisis.
EMERGENCY MUST HAVES
First Aid Kit – OSHA mandates first aid supplies must be on hand to supply medical assistance “commensurate with the hazards of the workplace.” checked and restocked every time something is used.
- Band Aids in various sizes
- Compression (Ace) bandages
- Gauze
- Antiseptic/Antibacterial cream
- Burn ointment
- CPR breathing barrier
- Disposable thermometers
- Tweezers
- Scissors
- Splints
- Instant cold packs and heating pads
- Pain reliever (both aspirin and non-aspirin ibuprofen)
- Tape
- Butterfly bandages
- Gloves – both latex and silicone-based as some people have latex allergies
Fire Extinguisher – A critical item to have placed near the break room or anywhere in the office where a fire could start. Perform a visual inspection should happen at least once a month (looking for a broken hose or any sign of damage) then inspected by a professional annually and have hydrostatic testing conducted every two years.
Disability Evacuation Equipment – If you have a disabled person in the office, you should purchase a stair chair for going down the stairwell. Also consider what fire alarm system you have, as employees who are deaf or hard of hearing will not be able to hear the siren.
ITEMS TO CONSIDER
Battery Powered Radio – Having an official NOAA weather radio is never a bad choice, especially if your office is located in an area prone to hurricanes or tornadoes. And if you are in such an area, keep multiple flashlights in the office in the event of a blackout. These are battery-powered devices, so it’s also a good idea to have extra batteries stocked along with…
Extended Shelter In-Place Supplies – a crisis may occur when your team cannot leave the office. Emergency food and water rations, portable showers, and emergency toilets are essential to surviving in a high-rise building, as you may be required to stay in place for a minimum of eight hours.
Automated External Defibrillator AED – thousands of employees experience cardiac function failures every year many of which result in deaths which could have been prevented by using an AED. If you acquire an AED for your office, you should consider who from your team should be trained to use the device. You may never know when you might need to use one, so having someone trained in this area before you acquire one, will mean that you’re sufficiently prepared in case of an life-threatening emergency. A piece of equipment similar to the Philips Onsite AED defibrillator could be a good place to start, as it can offer additional help during the process of CPR. It could help to save a life.
N95 respirator mask – this stronger version of a hospital mask filters particulate matter and different kinds of airborne chemical and biological elements. This is a filter, and not a “catch-all” but would be good to have on hand in the event of a chemical spill.
OTHER HELPFUL SUPPLIES
Basic Hygiene – Stocking contact solution, baby wipes, C Fold Paper Towels and feminine products are an extra measure of showing your employees you care for their overall well-being. Also, a sewing kit, useful in a pinch for numerous instances.
Extras! – Across the organization, employers should recommend individual employees have on hand extra doses of contacts, spare glasses, or critical medication for their personal use in the event of an emergency.
THINGS YOU REALLY DON’T NEED
Portable Generator – for the type of situation for your office, you should evacuate instead of attempting to shelter in place for the risk of carbon monoxide poisoning. Your building should already be supplied with a commercial generator in the event power goes out. If not, then it’s worth knowing that FW Power have a lot of used generators for sale that could be of use to your business. A portable generator shouldn’t be particularly necessary. If you’re using a generator at home, outside, well ventilated area.
“Imaginative” items – parachutes or repelling equipment might help one person in an extreme situation, but it’s far more likely that people would be harmed than helped.
Preparis Crisis Leaders and administrators can download their emergency kit checklist in their portal under Protocol & Policies. Our company offers a team available for consultative work to ensure your emergency preparedness plans are tailored to each and every employee’s needs.
Based on new injury statistics, an American is accidentally injured every second and killed every three minutes by a preventable event – a drug overdose, a vehicle crash, a fall, a drowning or another preventable incident. A total of 14,803 more people died accidentally in 2016 than in 2015, the largest single-year percent rise since 1936.