Equipment-Machinery – Stats and Facts
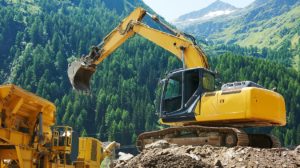
DID YOU KNOW?
The demand for machines in the U.S. by the automotive, construction, and food sectors, for example, ensures revenues within the machinery industry. In 2019, the estimated value of shipments of the industry was US$359.2 billion. 9.1% of the value of shipments was generated by the subindustry “Metalworking machinery manufacturing”.
Machinery manufacturing is one of the largest and most competitive sectors of the U.S. manufacturing economy. Exports of capital equipment totaled $141 billion in 2018 alone. Leading markets for U.S. Taken as a whole, the European Union was the U.S. machinery manufacturers’ third-largest market in 2018, after Canada and Mexico. Among the wide range of machinery manufactured in the United States, construction machinery, engine equipment, industrial process controls, agricultural equipment, and turbines and turbine generator sets led U.S. exports in 2018.
The economic impact of machinery manufacturing extends throughout the U.S. economy. Machinery industries provide essential and highly sophisticated technology for many other manufacturing and service industries. Industrial process controls and other automation technologies enable end-users to maximize the productivity of their equipment. Sales of many types of machinery are accompanied by a variety of high-value services as well, including specialized architecture, engineering, and logistics.
Tens of thousands of companies manufacture machinery in the United States. A majority of these manufacturers are small and medium enterprises (SMEs), but there are also many large, public companies and iconic American brands that trade on a global scale. Machinery is manufactured in almost every state, but production is concentrated particularly in the industrial Midwest, California, and Texas.
More than 1.1 million Americans are employed in the machinery manufacturing sector. These jobs are primarily in highly-skilled, well-compensated trades and professions. Leading employment categories include team assemblers, machinists, welders, tool-and-die makers, and mechanical and other engineers. Machinery manufacturing also supports the jobs of hundreds of thousands of Americans in a variety of other manufacturing and service industries.
In 2019, the breakdown of employer establishments in this industry was as follows: 36.4% of them were considered micro, employing less than five employees; small establishments accounted for 62.5%; and medium-sized establishments accounted for an additional 1.1% of the total number of establishments. Large employers, those with more than five hundred persons on payroll, accounted for 0% of the total establishments.
There are 3,399 industrial machinery and equipment wholesalers in United States.
Manufacturers in the United States account for 11.39% of the total output in the economy, employing 8.51% of the workforce. Total output from manufacturing was $2,334.60 billion in 2018. In addition, there were an average of 12.8 million manufacturing employees in the United States in 2018, with an average annual compensation of $84,832.13 in 2017.
Manufacturers help to drive the United States economy, with $1,397.03 billion in manufactured goods exports in 2018. That same year, $679.46 billion in exports was with our free trade agreement (FTA) partners. Small businesses comprised 96.60% percent of all exporters in the United States.
The 20 U.S. FTA partners purchased nearly 49 percent ($679.46 billion) of U.S. manufactured goods exports in 2018 – even though these countries represent only six percent of the world’s population and 10 percent of GDP.
Machines are a critical part of our lives. They take various forms and allow people to work with less effort and improve production efficiency. Numerous types of heavy construction equipment are available for use to contractors from different industries, such as mining and construction, for performing a wide variety of work activities. Different types of heavy construction equipment are used different types of projects, or work activities at different levels (Kazan, 2013). One of every five-workplace fatalities is a construction worker (OSHA, 2018). However, without proper safeguarding and controls, physical contact with machines and powered equipment can result in severe workplace injuries and deaths (Marsh and Fosbroke, 2015). The Bureau of Labor Statistics of fatal occupational Injuries identified 761 contact with object and equipment related deaths on construction sites in 2016. 970 person were also died in construction and extraction sector and when the incidence rates were examined, this sector becomes in third row, (12.4). McCann (2006) reported in the study about excavation industry between 1992-2006 years in the United States that moving vehicle incidents are 53 % and struck by objects are 24% of vehicle related deaths on construction site. Besides, the half of deaths in excavation industry are actualized about heavy equipment-related incidents on construction sites. Workers on construction sites often find themselves with dangerous and life-threatening conditions
KEEP IN MIND
Employees work with machines, tools and equipment every day. Workplaces couldn’t operate without them; however, interacting with them has potential for serious injuries or fatalities if they are not used and maintained properly.
The potential hazards are numerous, and include:
Safety hazards
- Contact with moving parts
- Contact with electricity, heat, fire, cold, and other energies
- Contact with pressurized gas or liquid
Health hazards
- Contact with harmful chemicals or biological hazards
- Contact with harmful noise, radiation, and/or vibration
- Exposure to ergonomic or MSD hazards
What the law says
Workplace machine safety law in Ontario is based on the Occupational Health and Safety Act (OHSA). Regulations specified under the Act that are applicable to specific workplaces.
In the Act, the sections dealing with responsibilities of employers (s.25), supervisors (s.27) and workers (s.28) set out general duties with respect to machine safety.
How machines, tools and equipment safety can affect your business
A safe environment is a productive workplace. Health and safety is not simply a legal obligation: it is a business opportunity. You can boost your bottom line by improving health and safety performance, which reduces the costs associated with avoidable losses and lost-time injuries, and leads to higher productivity.
Machinery can injure people by:
- crushing
- cutting
- shearing
- puncturing abrading
- burning
- tearing
- stretching.
Common injuries include:
- amputation
- crushing
- electric shock
- hearing loss
- ill health from hazardous chemicals or lack of oxygen
Causes and Types of Heavy Equipment and Machinery Accidents
Heavy equipment and machinery accidents can result from an endless list of factors. From operator error to equipment and machinery defects, if just one thing goes wrong, the consequences can be devastating. Some of the types of heavy equipment and machinery most-commonly involved in workplace accidents include:
- Backhoes and loaders
- Bulldozers
- Cherry pickers
- Combines and other farming equipment
- Cranes
- Dump trucks
- Electric hand trucks
- Excavators
- Forklifts
- Industrial and factory machines
- Trenchers
- Warehouse equipment and machinery
Some of the most-common factors involved in heavy equipment and machinery accidents include:
- Backing up
- Colliding with a stationary object
- Colliding with another piece of equipment
- Dropped loads
- Machinery entanglement
- Failure to check blind spots
- Objects falling from forklifts and other equipment
- Pinning workers between equipment and stationary objects
According to the U.S. Occupational Safety and Health Administration (OSHA), heavy equipment and machinery accidents are among the leading causes of serious and fatal accidents on construction sites, and safety standards governing the use of powered industrial trucks (such as forklifts) on jobsites are among those most-commonly violated by employers. Unfortunately, accidents happen even in the safest working environments, and this is why state workers’ compensation laws entitle employees to “no-fault” benefits for their on-the-job injuries.
We provide three levels of machine safeguarding assessments. Choose the level of assessment that fits your needs.
- Level 1: Machine hazard assessments (cost-effective solution for the entire plant)
- Level 2: Machine safety assessments (detailed assessment by a senior safety engineer)
- Level 3: Risk assessment (task-based risk assessment ANSI/RIA process led by a senior safety engineer)
Detailed descriptions of each level are shown below. Contact us for questions or a discussion on which type of assessment is right for you. We can provide example reports upon request.
We provide an extensive library of courses to support you in developing a culture of safety and a healthy workplace environment. Our courses are available as open registration public workshops, on-site training courses or on-demand e-learning programs. Course topics include:
- Machine guarding and safety
- How to conduct a risk assessment
- Alternatives to lock-out/tag-out (LOTO)
- U.S. machine safety standards and codes
- Risk assessment workshops
- OSHA 10 and 30
- Lock-out / tag-out safety (LOTO safety)
- NFPA 70E – electrical safety in the workplace
Advisory services
- Functional safety certification services – We help system integrators ensure the safe and reliable operation of subsystem components and assemblies.
- Safety system design review – including functional safety and control reliability reviews
- On-site validation
- Development of risk assessment program
- Other custom services
8 Facts About Machine Operators
When you think of manufacturing plants odds are images of gigantic conveyor belts and equipment come to your mind. Equipment which is computerized, mechanical and made up of many different parts. Well these pieces of equipment can’t just run themselves, they need individuals who can set-up and operate them.
Who are the individuals who run these machines? Well that would be machine operators!
In order to get a grasp of the workers at the heart of the manufacturing industry FoodGrads is exploring the careers of machine operators. You will get the facts on the challenging, hands-on work of machine operators and they control nearly every aspect of the manufacturing process.
1. Machine Operators operate machinery
Machine Operators (also known as production operators) are:
professionals who operate multi-function process control machinery or single function machines to process and package food or beverage products. They set up, maintain and disassemble their equipment based the on the requirements of a particular packaging job. Production operators perform necessary per-operational activities to ensure proper equipment startup and operation on multiple pieces of equipment. As well through-out the manufacturing run they keep a close-eye that the same conditions are observed through out.
Machine operators make sure their machines are working at full capacity, are stocked with the necessary materials and are well maintained. Doing so ensures that there is minimal downtime between the machines as downtime means the plant is not making money!
Finally, production operators rarely work by themselves and work in small teams within on their lines. Don’t forget they also work with quality control!
2. Machine Operators troubleshoot
If you talk to any machine operator you likely will hear that one of the most challenging parts of the job is troubleshooting equipment. The machines could have problems such as the weight of the product being higher than it should be. A machine operator may troubleshoot this problem by changing the settings by making adjustments to system components and run a test batch to determine if the changes have solved the issue.
If the issues are something the machine operator are unable to fix they will promptly communicate this with their production supervisor. To come up with viable option they may contact maintenance or even request a part from an outside company.
Troubleshooting is an important technical skill related to the machine operator job, and must be done on a regular basis to ensure the health and longevity of your machinery. If a problem occurs during a shift, your machine operator needs to know what needs to be done to fix it—and figure out the right procedure to do so in a relatively short amount of time. If your equipment is down for too long, it could result in damaging delays and setbacks in deadlines, making quick-thinking skills and troubleshooting a priority for your future employees.
To test the troubleshooting abilities of your potential candidates, you should create a scenario that they may run into during their daily activity that tests their critical thinking skills. You’ll get a better idea of how they perform under pressure, and how they might deal with an unexpected error in their workday.
3. Machine Operators have this education
In general, a production operator must have a minimum of a high school diploma or GED to qualify for the job. However, more specialized training may be necessary if the job demands working with high-tech equipment or machinery. Some companies provide on-the-job training so you don’t need the formal education. Operating machinery is a good role where some one can start and work their way up in a company. For example, you can start in production work up to a lead production hand and then production manager.
4. Machine Operators clean their machines
Machine Operators are required to clean their equipment and have it ready for a next production run. For example, if a manufacturing plant deals with various allergens on the same equipment the machine operator has to clean the equipment to prepare for the allergen switch over. This might be something as simple as doing a typical wash and sanitation. As well, they assist in other daily clean-up production duties such as sweeping the floors and taking out the trash.
5. Machine Operators work shift work
Many manufacturing plants have continuous operations which include days, night, afternoon, weekends and continental. It is not uncommon for machine operators to work different shifts depending on the production logs. It is usually only after working at a company for a while does an individual stick to a certain set schedule.
6. Machine Operators keep track of documents
Although machine operators spend a lot of their time running machines they also spend some of their time doing paper work. Production operators may be required to keep up with certain quality checks such as weight, percent oxygen and moisture content. Once they perform these quality checks they fill out the required forms. Furthermore, paperwork might include production logs to record how much product was actually produced in a day.
7. Machine Operators make quality issues
Quality assurance isn’t the only ones who help to ensure the quality of a product! Production operators evaluate the quality of a product as it proceeds through the production line by verifying product weight, colour, temperature and appearance in comparison to established parameters and quality markers. If they notice any issues, they will raise their concerns with their lead hand, supervisor and/or quality assurance personnel. They are the first line of defence so it is important that keep an eye out for potential defects.
8. Machine Operators have these set of skills
Being a production operator requires a range of skills however there are a few which are more essential than others. These skills include:
- Ability to work in a fast pace- Manufacturing plants are fast-paced environments and at times this can feel overwhelming. Machine operators are able to keep up in these environments because they are knowledgeable in their field. They also know the strength and weaknesses of their team members to help with the flow of their line.
- Attention to detail- It is necessary for machine operators to have an eye for detail because it ensures that operations run smoothly. If they do not pay attention to the detail, products could be made incorrectly, packaged in the wrong sized packaging or the be made in an unsafe manner.
- Good communication skills- To be an effective machine you need to be able to communicate information clearly. If they’re unable to communicate effectively about an issue in their department, it could result in a shortage of supplies, a broken down machine, or even a workplace related injury.
What you can do
Machinery and other workplace equipment can be dangerous if not used properly. Anyone using equipment in the workplace needs to be thoroughly trained in its operation and kept up to date. Here are other ways to help staff stay safe when using equipment.
- Keep the work area clean, tidy, well swept/washed, and well lit; floors should be level and have a non-slip surface.
- Do not remove any guarding devices; make sure that they are in position and in good working condition before operating.
- Follow lock-out procedures before measuring, cleaning or making any adjustments.
- Check and adjust all safety devices before each job.
- Wear appropriate personal protective gear as prescribed, including CSA-approved safety glasses with side shields (prescription eye wear is nota substitute).
- Ensure that all cutting tools and blades are clean and sharp; they should be able to cut freely without being forced.
- Ensure there is enough room around the machine.
- Ensure that all stationary equipment is anchored securely to the floor.
- Keep hands away from the cutting head and all moving parts.
- Avoid awkward operations and hand positions: sudden slips could cause the hand to move into the cutting tool or blade.
- Do not leave machines unattended: turn the power off.
- Avoid distracting an operator; horseplay can lead to injuries.
- Avoid wearing loose clothing, gloves, neckties, rings, bracelets or other jewelry that can become entangled in moving parts; confine long hair; do not use rags near moving parts of the machine.
- Return all portable tooling to their proper storage place after use.
- Clean all tools after use.
- Do not use cutting fluids to clean hands.
- Use a vacuum, brush or rake to remove any cuttings.