Facilities/Maintenance – Stats and Facts
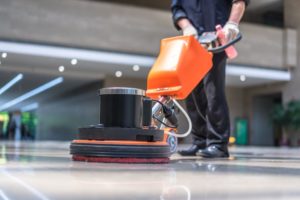
DID YOU KNOW?
Maintenance planning requires solid data, much of which you’ll obtain by collecting information on your own operations. It also helps to know what’s happening in the industry as a whole—that way, your own metrics are compared within a larger context. This ultimately helps you gauge where your own maintenance management processes are. You’ll get an idea of where you’re doing well and where you might need to make improvements in terms of maintenance management.
In addition, these statistics show just how important modern technologies are in terms of improving operational reliability, no matter how well you’re doing in comparison with the industry overall.
Maintenance costs, budgeting and spend
- Maintenance costs are estimated to range between 15% and 40%of total production costs (Dunn, 1987; Lofsten, 2000).
- Exterior building maintenance costs about $0.03 per square foot for industrial buildings (BOMA, 2018).
- Running a piece of equipment to the point of failure could cost up to 10 times as much as a regular maintenance program would (Buildings.com, 2018).
- Every $1 worth of maintenance deferred could quadruple to $4 in capital renewal costs later on (Biedenweg).
- Predictive maintenance is highly cost effective, saving roughly 8% to 12% over preventive maintenance, and up to 40% over reactive maintenance (according to the U.S. Department of Energy).
- Between 2004 and 2008, the U.S. spent about 57% of its transportation infrastructure budget on new construction projects. The 43% leftover was spent on maintaining the 98.7% of roads remaining.
- The U.S. has over 47,000 bridges that are considered to be in urgent need of repairs, while 38% of all America’s bridges need some form of repair work. It would take about 80 years to complete it all.
- The global market for enterprise asset management software is valued at $4 billion, and it’s expected to grow at a CAGR of 11% per year. At that rate, its value will have doubled to $8 billion by 2022.
- As of 2018, about 53% of facilities use a CMMS to monitor their maintenance. Additionally, 55% use spreadsheets and schedules, and 44% still use paper.
CMMS and Software Adoption
- In 2017, 78% of companies who used a CMMS to manage their assets reported seeing improvements in equipment life.
- Up to 80% of all attempted CMMS implementations fail.
- Perhaps coincidentally, about 80% of all CMMS users don’t use all the functions offered by the software.
- For one company in 2017, data visualization software reduced production hours by 320 hours while also increasing production by 15%.
Types of maintenance
- According to Plant Engineering’s 2018 maintenance survey, preventive maintenance is favored by 80% of maintenance personnel.
- In the same survey, it was shown that usage of predictive maintenance had risen from 47% to 51%, and that running equipment to the point of failure had dropped from 61% to 57%.
- Predictive Maintenance
- The overall use of predictive maintenance rose from 47% in 2017 to 51% in 2018, though preventive maintenance is still preferred by 80% of maintenance personnel.
- 80% of manufacturing plants use preventive maintenance, and over half use predictive maintenance with analytical tools.
- In 2012, the U.S. Bureau of Labor Statistics estimated that the nation would be short 10 million workers over the course of the following six years.
- Roughly 10% (and maybe even less) of industrial equipment ever actually wears out, meaning a very large portion of mechanical failures are avoidable.
- Predictive analytics yields a tenfold return on investment, and it results in a savings of 30% to 40%.
- As of 2018, the most common challenge facilities face is lack of resources, including human, technical, and strategic resources. The number of facilities who considered this a challenge was li 49%.
- Historically, total productive maintenance has been shown to increase plant capacity by over 10% and productivity by 50%, but over half of all attempts to implement TPM result in failure.
- 79% of businesses see predictive maintenance as the main application of industrial data analytics.
- Maintenance personnel
- The median salary of an industrial maintenance technician came out to $50,440 in 2017 (Bureau of Labor Statistics).
- The motor vehicle manufacturing industry pays the highest salary for maintenance technicians at $69,830 in 2017 (Bureau of Labor Statistics).
- Maintenance technicians are most widely employed by the plastics manufacturing industry at 3,830 The next runner up was motor vehicle parts manufacturing with 2,750 workers (Bureau of Labor Statistics).
- First line supervisors of maintenance workers tend to earn more, averaging at $68,120 per year (Bureau of Labor Statistics).
- Time management
- Out of an average working day, only 5% of the average maintenance worker’s time is spent performing productive tasks (Plant Services, 2003).
- Doing the math for an average maintenance technician based on average salary, the total time spent on unproductive tasks comes out to about $38,082 in labor costs per personnel per year.
- An estimated 20.9% of wasted time results from travelling to different areas in the facility, with an additional 19.8% resulting from waiting for instructions (Plant Services, 2003).
- Poor maintenance strategies can reduce a company’s production capacity by as much as 20% (Wollenhaupt, 2017).
- Production downtimes
- Roughly 82% of companies experienced at least one instance of unplanned downtime in the last three years (ServiceMax).
- A 2005 survey published by Thomas Industry Update found that the average cost of unplanned downtimes in the automotive industry amounted to $22,000 per minute.
- The average age of industrial assets in the United States is about 20 years, according to the Bureau of Economic Analysis. The number has grown significantly since 1990.
- Aging equipment is the leading cause of unplanned downtimes at 50%, with lack of time coming in at 14%, according to a 2016 survey by Plant Engineering.
- About 44% of all unscheduled equipment downtimes result from aging equipment, making it the leading cause of unscheduled downtime.
- Unplanned downtimes cost an estimated $50 billion every year.
- Overall, downtime costs most factories somewhere between 5% and 20% of their productive capacity.
- Safety
- Poor compliance with lockout/tagout standards ranked number five in OSHA’s most frequently cited violations in 2018.
- Up to 30% of all manufacturing deaths are related to a maintenance activity.
- Companies can save between 12% and 18% by using preventive maintenance over reactive, and each dollar spent on PM saves an average of $5 later on.
- Factories throughout the U.S. are estimated to be using about $40 billion worth of outdated equipment.
- Internet of Things (IoT)
- As of 2017, about 53% of companies adopted big data analytics, which includes predictive maintenance and IIoT technologies.
- By 2024, IIoT technologies are predicted to help create nearly $800 billion in economic value.
- Roughly 30% of all manufacturers have difficulty understanding IoT.
- Even so, as of 2018 nearly half of all manufacturers are placing greater emphasis on IIoT technologies.
- Worldwide spending on IoT technology is estimated to reach $1.2 trillion in 2022 with a CAGR of 13.6%.
- The number of connected devices in use worldwide is estimated to be over 17 billion, with 7 billion IoT devices.
- Maintenance Career Outlook
- The U.S. employs a total of over 80,000 machinery maintenance workers.
- The nation also has over 131,000 aircraft service technicians and mechanics.
- About 1.3 million people currently work as general maintenance workers, with 302,000 working in the real estate sector.
- The job outlook for maintenance professionals is projected to grow at about 8% over the next ten years.
- The average salary for a maintenance technician in 2019 is just under $39,000 per year.
- The top paying industry for machinery maintenance workers is the Federal executive branch at $72,350 per year as of 2019, followed closely by motor vehicle manufacturing at $71,330.
The following factors contributed to this outlook:
- Employment growth will lead to a moderate number of new positions.
- Several positions will become available due to retirements.
- There are several unemployed workers with recent experience in this occupation.
Here are some key facts about Facility operation and maintenance managers in the Regina – Moose Mountain region:
- Approximately 270 people work in this occupation.
- Facility operation and maintenance managers mainly work in the following sectors:
- Finance, insurance and Real estate and rental and leasing (NAICS 52-53): 16%
- Transportation and warehousing (NAICS 48-49): 12%
- Retail Trade (NAICS 44-45): 9%
- Wholesale trade (NAICS 41): 8%
- Information, cultural, arts, entertainment and recreation services (NAICS 51, 71): 7%
The number of U.S. employers offering flexible workplace options has grown by 40 percent in the past five years.
- As many as 30-40 percent of all U.S. workers today are contingent.
- Seventy-seven percent of workplaces in the U.S. use a combination of an open office and private, individual offices or a solely open office environment.
- Half of U.S. employees currently hold a job that is compatible with at least part-time remote work.
- Around 80-90 percent of U.S. professionals say they would like the ability to work remotely at least part-time.
- By allowing employees to work from home even half the time, the average company would save about $11,000 per person annually.
- Forty-four percent of companies offer a flexible work structure, such as allowing employees to choose when and where they work.
- The flexibility to make choices about where and how they work has a major impact on employee engagement, with 88 percent of highly engaged employees saying they can move around the workplace easily and choose where to work within the office based on what they’re doing.
- Forty percent of U.S. employees rate themselves as “engaged” and “satisfied” or “highly engaged” and “highly satisfied” with their workplace, placing them among the most engaged and most satisfied professionals in the world.
- Fifty-two percent of corporate executives say they plan to implement some level of unassigned seating in the workplace within the next three years.
- Fifty-one percent of all CRE leaders anticipate implementing a shared workplace model (such as a serviced office, co-working space, innovation center, or business incubator) in the next year.
- By 2020, available office space will decrease by 17 percent and there will be 15 percent fewer desks per employee, according to market research company Frost & Sullivan.
- CBRE’s Healthy Offices Research team found that promoting a healthy work environment with plants, circadian lighting and opportunities to meditate and exercise improved work performance by 22 percent.
Workplace Technology Statistics
Fifty-nine percent of executives plan to introduce mobile employee experience apps to help employees navigate an agile work environment.
Forty-eight percent of senior corporate real estate (CRE) executives utilize technology to capture more accurate data to support their business objectives.
Globally, 54 percent of employees have the option to bring their own device to work.
- Millennials, the first “digital native” generation, will make up 75 percent of the workforce by 2030.
- Fifty-eight percent of employees at “technology laggard” companies have negative feelings towards their employers.
- Nearly a third of non-IT-supported software downloads were the result of an employee needing an up-to-date tool the company didn’t provide or for which the company didn’t offer a comparable alternative.
- The shortcomings of employer-provided smartphones has resulted in 43 percent of employees using their personal devices for work, which makes the company more vulnerable to security risks.
- Despite the fact there are now more mobile devices in use than people on the planet, employers supply fixed technology solutions over mobile solutions at a ratio of 2:1.Over 80 percent of global employees are given a desktop computer and landline phone, but only 39 percent receive an employer-provided smartphone or laptop.
Smart Buildings and IoT Sensors
- Building connectivity is expected to add more than $25 billion to the building-controls market by 2025.
- Honeywell evaluated 500 buildings in seven U.S. cities and rated them on three key categories that define smart buildings: green, safe and productive. On a scale of 1 to 100, the average smart building score is 35.
- Deployment of IoT sensor technology in corporate real estate is expected to grow by 79 percent between 2015 and 2020.
- Using sensor technology to monitor energy usage in office buildings can reduce energy costs by as much as 20 percent.
KEEP IN MIND
You have facilities and they all need one thing…Facility Maintenance. That’s where we come in. In today’s tough economy it’s more important than ever that you work to get as much life out of your equipment and facilities as possible. That includes your Facility Maintenance. You also don’t want the burden of your own W-2’d employees draining your overhead as they are on the clock performing your Facility Maintenance. With Facility Maintenance USA you can “turn on the faucet” and “turn off the faucet” when you need a specific response to each of your Facility Maintenance needs.
This allows you to just pay for what you need. When you have an employee your challenge is justify his existence. When he finishes one task you need to quickly figure out the next one for him. If you don’t have anything for him to do next, then his overhead continues to run and the costs of the work that he has performed continue to increase. When you utilize Facility Maintenance USA you only pay for what you use.
Maintenance activities include keeping spaces, structures and infrastructure in proper operating condition in a routine, scheduled, or anticipated fashion to prevent failure and/or degradation. This includes one-to-one replacement of components and systems not requiring professional engineering or permitting. Maintenance activities do not involve a change in space classification or space use.
Examples of facilities maintenance include:
- Basic custodial services.
- Routine exterior painting of buildings and interior painting of public and common areas.
- General building repairs.
- Maintenance of building life-safety and security alarm systems, and systems such as heating, ventilation, air conditioning, plumbing, electrical and lighting.
- Pest control.
- Care of trees and shrubbery, lawns, sidewalks and snow removal.
- Maintenance and repair of door locks and door hardware.
- Some repair of classroom furniture.
Facility operation managers plan, organize, direct, control and evaluate the operations of commercial, transportation and recreational facilities and the included real estate. Maintenance managers plan, organize, direct, control and evaluate the maintenance department within commercial, industrial, institutional, recreational and other facilities.
Facility operation managers perform some or all of the following duties:
- Plan, organize, direct, control and evaluate the operations of commercial, transportation and recreational facilities and the included real estate
- Oversee the leasing of space in the facility and the included real estate and the development of marketing strategies
- Plan, organize and direct administrative services such as signage, cleaning, maintenance, parking, safety inspections, security and snow removal
- Plan, organize, direct, control and evaluate construction projects to modify commercial, transportation and recreational facilities and real estate
- Oversee the installation, maintenance and repair of real estate infrastructures including machinery, equipment and electrical and mechanical systems
- Plan and manage the facility’s operations budget
- Prepare or oversee the preparation of reports and statistics related to areas of responsibility
- Hire and oversee training and supervision of staff.
Maintenance managers perform some or all of the following duties:
- Direct the maintenance and repair of an establishment’s machinery, equipment and electrical and mechanical systems
- Develop and implement schedules and procedures for safety inspections and preventive maintenance programs
- Co-ordinate cleaning, snow removal and landscaping operations
- Administer contracts for the provision of supplies and services
- Plan and manage a facility’s maintenance budget
- Hire and oversee training and supervision of staff.
Where do they work?
Facility operation managers are employed by a wide range of establishments, such as airports, harbours, canals, shopping centres, convention centres, warehouses and recreational facilities.
Maintenance managers are employed by a wide range of establishments, such as office buildings, shopping centres, airports, harbours, warehouses, grain terminals, universities, schools and sports facilities, and by the maintenance and mechanical engineering departments of manufacturing and other industrial establishments.
Preventive maintenance means understanding that completing maintenance before a malfunction leads to disruption is better than waiting until equipment or asset failure. This is basic business, but it comes at the cost of increasing the volume of work when organizations already want to cut back on facilities spend. Thus, more companies are looking for ways to optimize operations through outsourcing. Consider the recent report by McKinsey & Company External Link:
“Companies have no shortage of options at their disposal to optimize facilities management expenditures. Outsourcing is a well-established strategy that’s on the rise thanks to an influx of vendors, while integrated approaches to facilities management, workplace strategy, and technology all hold promise. The global market for in-house and outsourced facilities management is estimated to reach $1.9 trillion by 2024. The outsourced segment accounts for more than half the total and has attracted a growing number of vendors with new service offerings.”
All companies are moving to utilize the latest technologies and strategies to stay competitive, and since competition depends on keeping costs under control, facilities management preventive maintenance is the natural path to lowering facilities spend. So, what are the top trends affecting preventive maintenance?
Top Facilities Management Preventive Maintenance Trends
Preventive maintenance trends for 2020 range from outsourcing through the requirement for a mobile-first approach, as follows:
- Outsourcing is the new normal of preventive maintenance scheduling and completion.
- More organizations will look for a single provider, read “manager,” approach to maintenance, streamlining maintenance management and avoiding the hassle of billing countless field service vendors and tracking invoices.
- Organizations will focus on improving the employee experience, as well as improving building occupant health through proactive, preventive maintenance.
- Flexible work arrangements will reduce the stress of performing and addressing maintenance needs.
- Maintenance will become data-focused and based on fact, not assumption.
- System integration will open new doors to savings and cost efficiency, taking advantage of the digital twin to all physical assets and using technology to optimize settings, lower maintenance frequency, and keep TCO in check.
- Mobile-first technologies will reduce barriers to better maintenance and visibility throughout it.
How to Improve Facilities Preventive Maintenance in 2020
Facilities Managers should follow these added tips to improve preventive maintenance and align organizational goals with the top trends in preventive maintenance through 2020:
- Connect facility assets through the IoT and focus on the use of IoT-enabled devices to improve space utilization and occupant experiences.
- Leverage a new computerized maintenance management system.
- Collect and apply data to understand the best-case maintenance schedule.
- Let data make the prioritization decisions and avoid budgeting crises.
- Integrate the CMMS with all facilities management platforms or service systems.
- Continuously build on a collaborative infrastructure to support the growth and continuation of facilities management preventive maintenance programs.
- Emphasize the value of remote access to asset maintenance schedules, as well as tracking compliance and device use in such activities to lower spend and boost ROI.