General Safety Rules
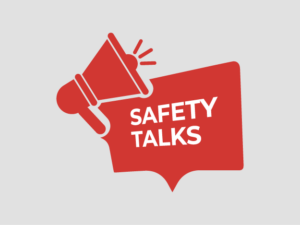
WHAT’S AT STAKE?
General Safety is a multi-disciplinary approach to developing and ensuring compliance with regulatory agencies, safe working practices, and maintaining the health and well-being of those employed in a particular occupation or workplace. Strategies to accomplish these goals maintain a strong focus on injury prevention through hazard identification, prevention and controls; education & training; audits & inspections; engineering modifications, and enforcement.
WHAT’S THE DANGER?
Machine Shop facilities must be kept in properly working status and maintained in safe working and handling environment by every personnel. Self-discipline and good working manner is the key to success for laboratory and the workshop. Any accident or mishap may damage equipment, cause injury or death. There are general rules and guidelines for the people working with mechanical devices to follow. There are also operational manuals and specific rules for every item of mechanical equipment to be followed by users. When you are operating a machine or a mechanical apparatus, you should always adopt a defensive attitude and be aware of the source of danger.
HOW TO PROTECT YOURSELF
There are general safety rules for people who work with mechanical devices and in potentially dangerous situations in their jobsite.
General Safety Rules
- All accidents, injuries and near misses must be reported to your supervisor, immediately.
- Immediately correct, or report any unsafe acts or conditions to your Supervisor, and warn any employees who may become involved.
- If you have any doubt regarding the safety of a job procedure, consult with your immediate supervisor before proceeding with the task.
- If an item of protective equipment is required by the job-site, or for the job you are doing, consider the use of that equipment as a condition of employment.
The following PPE must be worn:
- Steel-Toed Boots – Must be worn at all times on the job-site. Safety Boots must meet CSA standards, have penetration protection and have above the ankle support.
- Safety Vests – Conforming to WorkSafeBC Standards must be worn at all times on the job-site. “Spaghetti Strap Vests” are not acceptable.
- Hard-Hats – Must be worn at all times on all job sites/plants/yards.
- Hearing Protection – Must be worn when exposed to noise levels over 85 dBs. (e.g. Shouting instructions at 4’)
- Eye Protection – Must be worn when required by the job being performed: Grinding, welding, drilling, saw-cutting, jack-hammering, pressure washing…etc.
- Gloves – Must be worn when handling material likely to cut, puncture, burn or irritate hands.
- Life Jackets – Must be worn when working on barges without walls, within 10’ of an open dock, or in conditions that present the risk of drowning.
- Respirators – Must be worn when exposed to workplace atmospheric conditions that could result in injury: Saw-cutting/grinding concrete, painting, or handling chemicals.
- Fall Protection – Must be worn when working at heights of 10’ or greater.
- Clothing – Every employee must wear clothing appropriate for work, long pants and over-the-shoulder shirts must be worn at all times. Loose apparel and jewelry must be secured or removed, and long hair must be tied back.
- Inspect tools and equipment daily, ensure all guards and safety devices are in place and functional. Misuse or willful damage of company tools and equipment is strictly prohibited.
- Maintain good housekeeping in the workplace. Do not allow materials to gather on floors, platforms, ramps, stairs or walkways as to become a tripping hazard.
- Hazardous materials must be identified, stored and handled in accordance with the Workplace Hazardous Materials Information System (WHMIS) regulations in Canada or Globally Harmonized System (GHS) in the US.
- Never work alone in isolated areas unless arrangements have been made for periodic checks with another person.
- Underground utilities must be located with the use of utility maps and hand-digging procedures, prior to digging mechanically.
- Entry into excavations greater than 4 ft. deep is strictly prohibited, unless it is sloped or shored.
- Confined space entry procedures must be followed when entering a confined space.
- Fighting, scuffling, horseplay, practical jokes and theft are prohibited.
- The use of alcoholic beverages and drugs (including prescription or over the counter medications which may cause impairment) is strictly forbidden on the job or job-site. No person shall enter a job site while his or her ability to work is impaired.
- Smoking in non-smoking areas (offices, plant offices, shops, vehicles, flammable areas) is strictly forbidden. The only exception to this rule is if a worker is riding in a vehicle alone and there is adequate ventilation available.
- No worker shall ride on the outside of equipment unless the vehicle has been designed or modified for this purpose. All workers are to ride in the cabs of vehicles.
- Seatbelts must be worn when operating ROPS equipped machinery, and company vehicles.
- Never do maintenance or work under, on, or around a piece of running equipment. Shut it off and lock it out until your work is completed.
- No worker shall operate damaged tools, equipment or machinery. If it is not operating correctly, or needs maintenance, “tag it” out of service, fill out an equipment repair form, and return it to the Equipment Manager.
- No worker shall operate or use any equipment in a manner that endangers themselves or other workers. Only persons properly trained and authorized by their Supervisor shall operate any equipment or machinery.
- Workshop machinery fitted with safety devices must not be removed except under the direct supervision of the LS of the Workshop. Control of the safety equipment and its positions is under responsibility of the operators before using machinery.
- Tools are not to be stored on machine beds while the machine is running.
- Compressed air must never be used for blowing dust or swarf off clothing, skin or machinery. Incorrect utilization of compressed air may cause embolism, blindness or deafness to personnel and damage to nearby machinery.
- People who will use the machinery in mechanical laboratories must have training in machine tool operation.
- No person should work alone. In certain situations people may establish a buddy system where people located in other parts of the building are responsible for checking to see that the shop user is safe at all times.
- Comply with all the requirements of the Safety Program, WorkSafeBC and other applicable regulations.
FINAL WORD
The most important concept to remember is that you are responsible for your own safety and the safety of others. Most safety practices are common sense. Unfortunately, they can be forgotten or overlooked unless you make safe practices a habit or an instinct.