Hand Safety – Spanish
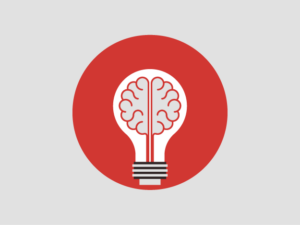
Key Takeaways:
– Evaluating common hazards to the hands
– Describing methods and devices used to prevent hand injuries
– Learning the differences in hand protection devices (gloves)
Course Description
There are more than one million emergency room visits per year because of occupational hand injuries.
Regardless of the work you do, likely you use many tools in your job. As well, at many times your hands are the tools for the job, but the rules you’d use to take care of other tools also apply to your hands. One example of a rule is to always use the correct tool for the job. Using a tool for something other than it was intended is called “misuse.” It’s not worth it to risk your hands when the appropriate tool exists for the job.
To prevent hand injuries, you need to know the hazards involved in your job and how to avoid them.
Often, injuries happen when workers have bypassed or deactivated safety features on equipment. Maybe it feels pointless, but guards and other safety features serve an important purpose — do not tamper with them or modify controls, they protect you from specific injury, no matter how inconvenient they may appear.
As well, never take off personal protective equipment (PPE). Frostbite often occurs when a worker removes their protective gloves in an extremely cold environment. You might believe some task that requires greater finger dexterity than can be accomplished with your gloves on, and it won’t take long, but this miscalculation creates serious risk.
Various injuries come from employees not following process instructions. Typically, this happens from boredom with a routine task or a mistaken sense that the worker is experienced enough to bypass instructions.
Also, distractions such as a wandering mind or wandering eyes can lead to injury. When hazards are close, you need to always focus on the task and keep your eyes on the job. Never rush and if you get frustrated, stop and take a break. Getting frustrated often leads to carelessness and injury.
Lastly, never think you can bend the rules “just this once.”
In total, there are three types of safety controls employers can use to prevent hand injuries: engineering controls, administrative controls and personal protective equipment (PPE).
– Engineering controls significantly reduce hazards through safeguards built specifically to mitigate certain hazards (i.e. equipment that has built-in measures to protect the user). The preferred way to eliminate or reduce hazards is always engineering controls, because the safety measure is built-in; the first line of defense. Routinely, engineering controls need to be calibrated and maintained to ensure they work the correct way, every time.
– Administrative controls are protocols used to protect your workforce. Although engineering controls are preferred, administrative controls benefit when engineering controls cannot be implemented, or if engineering controls are unable effectively reduce risk alone. It is critical that employees follow the policies safety professionals prescribe because administrative controls will not eliminate hazards. An important illustration is the adoption of a 100% glove use policy — gloves are used for all tasks.
– Personal protective equipment reduces exposure to hazards when engineering and administrative controls are not feasible or are not sufficient to bring hazards down to acceptable levels. Gloves are the primary piece of PPE to protect hands from specific injuries. After engineering and administrative controls, PPE is considered the third line of defense.
An incredibly effective way to protect your hands is to wear gloves when appropriate. The U.S. Bureau of Labor Statistics states that 70% of workers who get hand injuries were not wearing gloves. Those who were wearing gloves, the remaining 30%, were injured because their gloves were inadequate, damaged, or the wrong type of glove for the hazard.