Machine Guarding 2 Meeting Kit
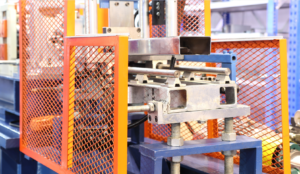
What’s At Stake
Machine guarding provides a means to protect humans from injury while working nearby or while operating equipment. It is often the first line of defense to protect operators from injury while working on or around industrial machinery during normal operations.
What’s the Danger
HAZARDOUS MECHANICAL MOTIONS AND ACTIONS
A wide variety of mechanical motions and actions may present HAZARDS to the operator and recognizing hazards is the first step toward protecting operators from the danger they present.
The Basic Types of Hazardous Mechanical Motions and Actions
Motions. Rotating (including in-running nip points). Reciprocating. Traversing
Actions Cutting. Punching. Shearing. Bending
HOW TO PROTECT YOURSELF
METHODS OF SAFEGUARDING. There are five (5) general types of machine safeguards that can be used to protect workers and personnel.
- Guards – these are physical barriers that prevent contact. They can be fixed, interlocked, adjustable, or self-adjusting.
- Devices – these limits or prevent access to the hazardous area. These can be presence-sensing devices, pullback or restraint straps, safety trip controls, two-hand controls, or gates.
- Automated Feeding and Ejection Mechanisms – These eliminate the operator’s exposure to the point of operation while handling stock (materials).
- Machine Location or Distance – this method removes the hazard from the operator’s work area.
- Miscellaneous Aids – these methods can be used to protect both operators and people in the immediate vicinity of operating machinery. Examples include shields to contain chips, sparks, sprays or other forms of flying debris; holding tools that an operator can use to handle materials going into the point of operation; and awareness barriers to warn people about hazards in the area.
SAFEGUARD REQUIREMENTS
Prevent Contact: The safeguard must prevent hands, arms, and any other part of a operator’s body from making contact with dangerous moving parts.
Secure: Operators should not be able to easily remove or tamper with the safeguard, because a safeguard that can easily be made ineffective is no safeguard at all.
Protect From Falling Objects: The safeguard should ensure that no objects can fall into moving parts.
Create No New Hazards: A safeguard defeats its own purpose if it creates a hazard such as a shear point, a jagged edge, or an unfinished surface that could cause a laceration.
Create No Interference: Any safeguard that impedes an operator from performing the job quickly and comfortably might soon be overridden or disregarded.
TYPES OF BARRIER GUARDS
Barrier Guards are appropriate safeguards for full revolution and part revolution mechanical power presses. They are designed to keep the operator’s hands and arms from entering the “danger zone” as prescribed by the machine. Barrier guards are usually the first point-of-operation safeguard considered for machines.
BARRIER GUARD REGULATIONS
- Barrier guards on power presses must prevent the entry of hands or fingers into the point of operation by reaching through, over, under or around the guard.
- The barrier guards must conform to maximum permissible openings tables.
- The barrier guard itself must not create pinch points between the guard and moving machine parts.
- The guard must not be easily removable.
- The guard must not interfere with machine inspection.
- The barrier guard must offer maximum visibility of the point of operation consistent with the other requirements.
INSPECTION/RISK/GUARDS
Prevent machine by injuries using guarding devices. The challenge is to decide which guards to use to control the risks from the hazard assessment. Verify guards are:
- Effective in keeping the worker’s body, hair and clothing from contacting moving parts.
- Firmly secured so that workers can’t easily remove them.
- Free of jagged edges, shear points, unfinished surfaces, and other hazards.
- Allowing workers to do their job quickly and comfortably – if they don’t, workers may try to remove them.
BEST MACHINE GUARDING SAFETY PRACTICES
To avoid potentially life-threatening injury, workers should receive proper training before operating any machines or power tools. workers must never operate machinery without prior training. Workers must:
- Inspect all tools and guards before each use
- Follow all proper lockout/tag out procedures when necessary
- Use proper procedures when setting up a machine, adjusting a machine, clearing jams, and cleaning or lubricating parts
- Never remove guards while operating a machine
- Tag all damaged guards and machinery “Do Not Use” and report them immediately
- Report machine hazards and other workplace hazards to their supervisor.
- Use or operating machinery in a safe manner.
- Use or wearing protective devices or clothing required by the employer.
FINAL WORD
Machine safety requires a combination of proper training, safeguards, good judgment, and concentration. Even simple machines can pinch, cut, or crush. Allowing yourself to become distracted, even for a second, can have serious consequences for you or the people you work with.