Noise and Hearing Protection Safety Talk
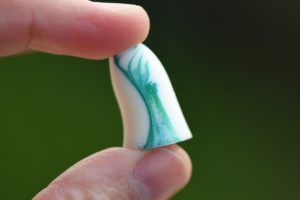
WHAT’S AT STAKE?
When does hearing loss, or hearing impairment, become the result of a work-related exposure? After all, we live in a world where loud noises are common, like from heavy city traffic, or even the music so kindly being shared through the open windows of the car stopped next to you. And there’s often that person who thinks headphones are speakers and has the music playing loud enough that it can be heard by everyone in the room. Loud noise is common. Loud noise can lead to hearing loss.
There is no denying that the tools that we use in our lines of work create loud noise, too, but that doesn’t necessarily mean that employees will lose their hearing. With the proper workplace hearing protection controls in place to eliminate, reduce, and protect against potentially damaging noise exposures, we reduce the chances that our employees will experience occupational hearing loss.
WHAT’S THE DANGER?
UNDERSTANDING HEARING DAMAGE
Hearing loss can occur when exposed to 85 decibels of noise averaged over 8 hours. Normal conversations typically occur at 60 decibels, well below the hearing loss threshold. Remember those headphones used as speakers? That music was probably playing at full volume, which can often register as 105 decibels. For every 3 decibel increase past 85 decibels, hearing loss can occur in half the amount of time. So it only takes 4 hours of exposure to 88 decibels for hearing loss to occur, and 2 hours of exposure to 91 decibels. Once noise levels exceed 100 decibels, a person can suffer hearing damage in as little as 15 minutes. The louder the noise, the faster hearing loss occurs.
WORKPLACE NOISE LEVELS
Where do the tools and environments where we work fit into this picture?
- Air compressors from 3 feet away register 92 decibels, which would take less than 2 hours to cause hearing loss
- Powered drills register 98 decibels, which would cause damage after 30 minutes
- Typical factories often register at 100 decibels – that’s 15 minutes of exposure
- Powered saws can reach 110 decibels from 3 feet away, which could cause permanent hearing loss in under 2 minutes
In short, if workers are exposed to these noise levels without protection, then hearing loss is very likely. The only way to know the exact noise levels that workers are exposed to is to conduct noise monitoring using specialized equipment, though this is only required when exposures are at or above 85 decibels. Some indications that noise levels may be this high are if employees complain about the loudness of the noise, if there are signs suggesting that employees are losing their hearing, or if the noise levels make normal conversation difficult. Also consider that these conditions may not occur across the entire work site, but may be limited to a specific task or piece of machinery.
HOW TO PROTECT YOURSELF
THE IMPORTANCE OF HEARING PROTECTION IN THE WORKPLACE
The best protection we can provide is to eliminate the hazard, by eliminating the need to work with the tools or in the environments that create these noise exposures. Realistically, though, this isn’t always possible. We can also work to reduce the noise levels that employees are exposed to. Some tools and machines are available that are designed to operate at lower decibels, therefore reducing the risk of hearing loss. We can also implement administrative controls, such as placing a cap on the number of hours that an employee can work in a high decibel environment, or limit the hours working with specific tools and equipment.
The final line of protection is PPE that meets OSHA hearing protection requirements. Ear plugs and ear muffs can reduce the decibel exposures, providing protection against hearing loss. Ear plugs provide the greatest amount of protection as long as they are inserted correctly. Therefore, employees need to be trained to wear them correctly when they are used. Ear muffs can also reduce the decibel exposures, though not to the extent that ear plugs can. They are easier to wear correctly, though, which is why some workers prefer them.
Some high decibel exposures may be unavoidable to perform the tasks necessary for our operations, but that doesn’t mean that we can’t take steps to protect employees and their hearing while at work. What they do in their free time, like attending a rock concert (which can peak at 130 decibels), becomes their choice.
- earmuff seals are undamaged;
- the tension of the headbands is not reduced;
- there are no unofficial modifications;
- compressible earplugs are soft, pliable and clean.
WHAT CHECKS HAVE TO BE MAKE?
You need to make sure that employees use hearing protection when required to. You may want to:
- include the need to wear hearing protection in your safety policy. Put someone in authority in overall charge of issuing them and making sure replacements are readily available;
- carry out spot checks to see that the rules are being followed and that hearing protection is being used properly. If employees carry on not using it properly you should follow your normal company disciplinary procedures;
- ensure all managers and supervisors set a good example and wear hearing protection at all times when in hearing protection zones;
- ensure only people who need to be there enter hearing protection zones and do not stay longer than they need to.
HEARING CONSERVATION PROGRAMS IN CANADA
Eight jurisdictions specifically require a hearing conservation program when:
- Noise exceeds the jurisdiction’s occupational exposure limit (four jurisdictions: Federal, British Columbia, Newfoundland and Labrador, and Prince Edward Island).
- Noise exceeds 85 dBA (three jurisdictions: Northwest Territories, Nunavut, and Saskatchewan).
- There is excess noise (one jurisdiction: Alberta).
Six jurisdictions do not have a specific requirement for a hearing conservation program (Manitoba, Ontario, Quebec, New Brunswick, Nova Scotia, and Yukon).
However, as per Occupational Health and Safety legislation across Canada, employers have a duty to provide a safe work environment and take all reasonable precautions to protect the health and safety of employees and others in the workplace. This duty is known as due diligence. To exercise due diligence, an employer should work with the health and safety committee (or representative) to create and implement hearing conservation program when needed. Check with your jurisdiction for more guidance.
WHEN IS A HEARING CONSERVATION PROGRAM RECOMMENDED?
The employer should conduct a noise assessment at the workplace, according to the CSA Standard Z107.56 Measurement of Noise Exposure, if:
- a worker is or is likely to be exposed to noise in excess of 80 dBA
- there is an alteration, renovation or repair of the workplace
- new equipment introduced in the workplace, or
- a modification done to a work process, that may result in a significant change in a worker’s exposure to noise.
Note the requirement when to conduct a noise assessment (e.g., dBA level) may vary from jurisdiction. Conducting an assessment at an action level of 80 dBA provides more protection.
THE ELEMENTS OF A HEARING CONSERVATION PROGRAM
If noise monitoring confirms that workers are exposed to noise levels at or above 85 dBA, a hearing conservation program should be developed and implemented. The program includes a policy and procedure. The CSA Standard Z1007 Hearing Loss Prevention Program Management recommends that a hearing conservation program include the following elements:
- Hazard identification and exposure monitoring
- Control methods (using the hierarchy of controls)
- Hearing protection devices (selection, use, and maintenance)
- Audiometric testing
- Hazard communication, education, and training
- Recordkeeping, and
- Continuous monitoring and improvement (program review).
CONTROL NOISE EXPOSURE
The employer should make sure that, if reasonably possible, measures are taken to reduce noise levels using the hierarchy of controls in the following order before providing hearing protection devices:
- Eliminate the hazard
- Engineering control
- Substitution of equipment, and
- Administrative
THE NEED FOR HEARING PROTECTION DEVICES
The majority of the jurisdictions require that employers provide hearing protection devices when noise levels are at or above 85 dBA. The value of 85 dBA is also based on good practice guidelines set out by organizations such as the Centers for Disease Control. CSA Standards Z94.2 Hearing Protection Devices – Performance, selection, care, and use and Z1007 Hearing Loss Prevention Program Management also recommend that hearing protection devices be used when engineering controls or administrative controls are not practicable or do not reduce noise exposure to acceptable levels (i.e., below 85 dBA).
THE WHAT TO DO WHEN HEARING PROTECTION IS NEEDED
The employer should make sure that the selection, care, and use of hearing protection devices meet the specifications outlined in the CSA Standard Z94.2.
The employer should make sure that a worker using the hearing protection device is adequately trained and instructed by a competent person in selection, fit, use, care, maintenance, and inspection.
The choice of hearing protectors is a personal one, and depends on a number of factors, including but not limited to acoustics, comfort, and the suitability of the hearing protector for both the worker and the environment. Where protectors must be used, provide a choice of different types when possible. Having choice encourages use, and protection can only be effective if it is properly and consistently used. Anatomy of the ear and ear canal can vary significantly making comfort and individual preferences important.
AUDIOMETRIC TESTING
Audiometry is an important part of the hearing conservation program. It is the only way to determine if a hearing loss is occurring or being prevented. Although existing hearing loss cannot be cured, the data can be used to:
- Identify persons for follow-up and counselling
- Determine trends
- Make decisions on control measures
- Motivate employees to use protective equipment
- Create education opportunities
- Trigger changes in the program
Generally speaking, audiometric testing is recommended when a worker is exposed to noise levels greater than 85 dBA. Audiometric testing should be conducted according to CSA Standard Z107.6 Audiometric Testing for Use in Hearing Loss Prevention Programs, which outlines specifications for the testing facility, the equipment used, and those in charge of conducting audiometric tests.
The CSA Standard Z1007 Hearing Loss Prevention Program Management recommends that audiometric testing involves:
- an initial hearing test, and
- a hearing test at least once every 12 months after the initial test, or
- a hearing test more frequently should the noise level exceed 105 dBA.
RECOMMENDATIONS / OR HAZARD COMMUNICATION
If it is not practicable to reduce noise levels to or below the noise exposure limits, the employer should post clearly visible warning signs at every approach to an area in the workplace in which the sound level:
- Exceeds 80 dBA – clearly marked with a sign that states “Warning” and identifies the range of noise levels
- Exceeds 85 dBA – clearly marked with a sign that states “Warning” and specifies that workers are required to wear single hearing protection device
- Exceeds 105 dBA – clearly marked with a sign that states “Warning” and specifies that workers are required to wear double hearing protection devices
WORKER EDUCATION AND TRAINING
Education and training should be provided to workers who are required to wear hearing protection devices. The education and training should cover all elements listed in CSA Z94.2 (i.e., selection, fit, use, care, maintenance, and inspection). The education and training should be repeated, as recommended in the Standards, at regular intervals and at least once every two years.
INFORMATION ABOUT EDUCATION AND TRAINING
- Why use hearing protection
- When should protective equipment be worn, in what work areas, during what work activities
- How should hearing protectors be selected and worn
- Who is responsible for taking care of the protective equipment
- How to take care of the protective equipment (storage, cleaning, etc)
- Company policy requirements for noise control and hearing conservation
- Legislative requirements
WHAT TYPE OF RECORDS AND DOCUMENTS SHOULD BE KEPT?
Keeping records of your assessment and any control measures implemented is very important. You may be required to store the records and documents for a specific number of years. Check for local requirements in your jurisdiction.
The level of documentation or record keeping depend on:
- Level of risk involved.
- Legislated requirements.
- Requirements of any management systems that may be in place.
RECORDS SHOULD SHOW THAT YOU:
- Conducted a good hazard review.
- Determined the risks of those hazards.
- Implemented control measures suitable for the risk.
- Reviewed and monitored all hazards in the workplace.
PROGRAM REVIEW OR EVALUATION
A program review or evaluation is done by auditing each of the program’s steps and seeing how well they are being executed. For example, ask the following questions:
- Are all elements or steps in place?
- Is it necessary to re-test or monitor the noise exposures?
- Are there periodic education and training sessions?
- What are the results from the audiometric tests?
- Have changes in processes or equipment resulted in reduced hearing losses?
- Do existing noise controls appear to be in good working condition and being used?
- Have any modifications been made to controls, possibly reducing their effectiveness?
- Is hearing protection available? Is it stored and maintained properly?
- Are workers wearing their protection? Have they noted any issues?
- Are warning signs posted where they are necessary?
- When new machinery or equipment is being purchased, is “buying quiet” considered in the decision process?
- Are further changes necessary to protect workers?
The program should be reviewed periodically to see if there is a need for changes.
FINAL WORD
Noise is unwanted sound. Noise can harm human hearing. Noise has at least two measurable effects on humans. Hearing Loss can be temporary or permanent and can be measured. Physical Effects that may include fatigue, tension, increased blood pressure and stomach disturbances.