Non Sparking Tools – Quick Tips
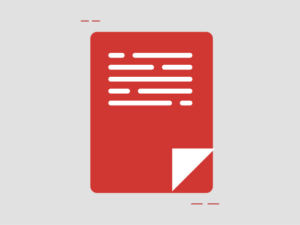
Non-sparking tools are made of materials that do not contain iron (non-ferrous metals) and therefore the risk of a spark being created while the tool is in use is reduced. Non-sparking tools protect against both fire and explosion in environments that may contain flammable liquids, vapors, dusts or residues. When working in confined spaces and areas where flammable gases or dusts are present, using a non-sparking tool is the best practice.
Common materials used for non-sparking tools include brass, bronze, copper-nickel alloys, copper- aluminum alloys or copper-beryllium alloys. Beryllium alloys are less favorable due to the potential toxicity of beryllium dust. Non-metals such as wood, leather and plastics can also be used to create non-sparking tools.
Some common tools that are available in a non-sparking option include hammers, axes, pry bars, chisels, utility knives, mallets, pliers, screwdrivers, sockets and wrenches. Non-sparking polypropylene shovels are often used for hazardous material spill clean-up.
Because non-sparking tools are non-ferrous, they are softer than standard tools which are usually made of a high strength alloy steel. This may cause non-sparking tools to wear more quickly than their steel counterparts.
Regulations and Compliance
The Occupational Safety and Health Administration’s (OSHA’s) Hand and Portable Powered Tools and Equipment standard [29 Code of Federal Regulations (CFR) 1910.242(a)] states “Each employer shall be responsible for the safe condition of tools and equipment used by employees, including tools and equipment which may be furnished by employees.” Maintaining non-sparking tools in a safe condition is vitally important.
Ampco Safety Tools, a leading manufacturer of non-sparking tools, offers common-sense guidelines for proper use and maintenance of non-sparking tools:
- Keep non-sparking tools clean and free from ferrous or other contaminants, which may impair the non-sparking properties.
- Do not use non-sparking hand tools in direct contact with acetylene, due to the possible formation of explosive acetylides, especially in the presence of moisture.
- During normal use, all hammers and chisels will progressively develop some damage to the striking faces of hammers or the cutting edge and striking end of chisels. As part of the normal operating and safety procedures, these tools should be returned to the workshop, as with steel tools, to have the faces and heads redressed. This is essential to prevent eye damage resulting from chips detaching from the item during use.
- Do not store hammers and other hand tools fitted with wooden handles in places where the handles may dry out and shrink. This will increase the risk of the handle breaking or the head becoming loose.
- Avoid overstrikes, causing damage to the shaft. Replacement handles are often available from the manufacturer, and should be fitted by a competent operator, using an approved method of fitting and paying particular attention to the fitting of the wedges.
- Fiberglass handles can offer advantages over wooden handles in terms of breaking stress and tolerance for adverse environmental conditions. Fiberglass shafts fail progressively, rather than catastrophically, reducing the risk of sudden failure, injury or damage.
- When selecting a wrench, the jaw opening should have a close and tight fit on the head of the nut or bolt to which it is being applied. This is especially true with non-sparking tools, as they typically do not have the hardness of steel tools.
- Tools are designed for specific use. As with any tool, additional torque should not be applied through the use of “cheater bars.” In addition to the probability that the tool will be damaged, this is a dangerous practice for the safety of the operator. Wrenches should not be used as levers; screwdrivers not as chisels, and so on.
- The accepted standards of safety and maintenance for common steel hand tools must also be adopted with non-sparking hand tools, in addition to any specific recommendations resulting from the alloys used.
- When sharpening non-spark safety tools, follow normal safety procedures, such as the provision of eye and face protection, adequate extraction and dust collecting facilities.
OSHA’s information booklet titled “Hand and Power Tools” (Document 3080) states: “Iron or steel hand tools may produce sparks that can be an ignition source around flammable substances. Where this hazard exists, spark-resistant tools made of non-ferrous materials should be used where flammable gases, highly volatile liquids, and other explosive substances are stored or used.”
In the Confined Space standard, 29 CFR 1910.146 Appendix D – Confined Space Pre-Entry Check List, under section 9 – Equipment, reference is made to having “All electric equipment listed Class I, Division I, Group D and Non-Sparking Tools.”
In response to the toxicity of beryllium and potential exposure in the workplace using copper-beryllium alloy non-sparking tools, OSHA has recently issued new standards to control exposure to all beryllium and beryllium compounds:
- General Industry: 29 CFR 1910.1024
- Construction Industry: 29 CFR 1926.1124
- Maritime Industry: 29 CFR 1915.1024
These standards target employees exposed to beryllium or beryllium compounds that can be inhaled. The objective of the standards is to prevent chronic beryllium disease and lung cancer. If conditions exist where non-sparking tools can produce particles small enough to be inhaled such as grinding (sharpening, removing burrs or mushroom heads), sanding, chipping, drilling or heating of the non-sparking tool further action may be needed under these new rules. Refer to the OSHA beryllium landing page for more details.
There are many standards for Hand Tools that manufactures follow. The American National Standards Institute (ANSI) Committee B107 establishes safety considerations for the hand tool family and includes:
- 4 – Driving and Spindle Ends for Portable Hand, Impact, Air, and Electric Tools (Percussion Tools Excluded)
- B107 – Gages and Mandrels for Wrench Openings
- 100 – Flat Wrenches
- 110 – Socket Wrenches and Attachments
- 300 – Torque Instruments
- 400 – Striking Tools
- 410 – Struck Tools
- 500 – Pliers
- 600 – Screwdrivers
Buying tools that meet the ANSI B107 series of standards is assurance that you can expect a high level of performance and safety from these tools.
Selection of Non-Sparking Tools
In general, non-sparking tools should be used in any environment where ignition sources are a concern. Applications include, but are not limited to:
- Maintenance and repair operations in environments that may contain flammable liquids, vapors, or combustible dusts or residues
- Collection, holding and transfer of flammable liquids
- Hot work
- Work in confined spaces
- Transportation (airports, railroads, tanker trucks, shipyards)
- Chemical, petrochemical and gas operations
- City, State and Federal Governments (utilities, waste management, hazardous material response, weapons of mass destruction)
Selection of the appropriate tool for the task is vital. Tools must be used only for the purpose for which they were designed. The Hand Tool Institute (HTI) offers many safety education materials that aid in proper tool selection on their Safety Education Program web page.
Commonly Asked Questions
Q: How do I store and maintain my non-sparking tools?
A: Keep non-sparking tools clean and free of ferrous metal contamination which can reduce their non-sparking ability. Avoid contact with acetylene which can form explosive acetylides, especially in the presence of moisture. If damage has occurred to the striking face of hammers or to the edge of chisels, the tools should have the faces and heads redressed. Do not store hammers and other hand tools fitted with wooden handles in places where the handles may dry out and shrink. This will increase the risk of the handle breaking or the head becoming loose.
Q: Why does a non-sparking tool specify that it is beryllium free?
A: The non-sparking tool industry is sensitive to the potential toxicity of beryllium dust, mist, and fumes that may occur while working with the softer metals in a non-sparking tool. Other non-sparking metals do not carry that same concern.
Sources
Occupational Safety and Health Administration (OSHA), Hand and Power Tools, Document 3080, 2002
The information contained in this article is intended for general information purposes only and is based on information available as of the initial date of publication. No representation is made that the information or references are complete or remain current. This article is not a substitute for review of current applicable government regulations, industry standards, or other standards specific to your business and/or activities and should not be construed as legal advice or opinion. Readers with specific questions should refer to the applicable standards or consult with an attorney.
Source: Grainger Know How – https://www.grainger.com/know-how