Pre-Operational Inspection of Equipment Meeting Kit – Spanish
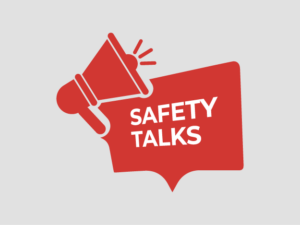
QUÉ ESTÁ EN RIESGO
LA INSPECCIÓN DE SEGURIDAD PREOPERACIONAL
“Una onza de prevención vale más que una libra de cura”. Adquirir el hábito de inspeccionar regularmente todos los equipos es una medida preventiva sencilla pero importante y debería formar parte de la rutina diaria de todo operario antes del turno.
Una herramienta útil es la lista de comprobación de la inspección preoperacional. Implementar el uso de un sistema de lista de comprobación en papel recuerda al operario que debe realizar regularmente todas las comprobaciones previas al turno, garantiza que los problemas se documenten y se comuniquen a los supervisores, y ayuda a señalar cuándo y cómo se han producido los cambios en el estado del equipo.
- Realizar la comprobación previa al trabajo es importante para la seguridad del operario y de todas las personas que se encuentran en su entorno de trabajo. Lamentablemente, esta comprobación de seguridad suele olvidarse o ignorarse. No todos los operarios son conscientes de los elementos que deben comprobarse antes de poner en marcha su máquina y comenzar a realizar sus tareas diarias.
- El operador del equipo puede evitar el tiempo de inactividad, prolongar la vida útil y garantizar un funcionamiento más eficiente con sólo unos minutos de inspección preventiva tanto antes como después de la operación.
- La clave es la coherencia. Estas inspecciones deben estar arraigadas en todas las partes y realizarse todos los días.
COMO PROTEGERSE
LA LISTA DE COMPROBACIÓN DE LA INSPECCIÓN
- Compruebe si los neumáticos, las llantas o el tren de rodaje presentan daños o un desgaste anormal y elimine los residuos. Al igual que no se puede trabajar a pleno rendimiento con un pie roto o con unos zapatos rotos o que no encajan, una máquina puede verse afectada por la ineficacia de los neumáticos o las orugas sobre las que se asienta. Identifique e informe de cualquier daño o daño potencial.
- Compruebe los niveles de fluidos: aceite del motor e hidráulico, gasóleo y líquido de escape (DEF), y refrigerante. Los fluidos son el alma de cada máquina y requieren niveles específicos para funcionar correctamente. Una caída repentina de los niveles de fluidos puede indicar cualquier problema en la máquina que requiera atención inmediata (mangueras reventadas, fugas en el filtro, etc.).
- Limpie los residuos acumulados alrededor del radiador y otros componentes del motor. El motor está formado por piezas móviles y correas que generan calor y fricción, y los sistemas diseñados para refrigerar el compartimento del motor necesitan espacio para respirar. Es importante comprobar y eliminar cualquier desorden o material del lugar de trabajo que pueda haberse colado en el compartimento del motor.
- Compruebe que los filtros de combustible, aceite, aire y otros no presentan daños ni fugas.
- Compruebe las correas (alternador, ventilador, etc.). Una correa desgastada y deshilachada es otro elemento de desgaste relativamente fácil de sustituir.
- Identifique los puntos de engrase y su frecuencia.
- Compruebe que no hay fugas o charcos de líquido alrededor y debajo de la máquina.
- Compruebe las conexiones hidráulicas auxiliares y la presión.
- Compruebe si hay nuevos signos de daños estructurales, arañazos o abolladuras en la máquina.
- Compruebe si hay daños en las herramientas de enganche al suelo (cazos, dientes, etc.).
- Inspeccionar el montaje de los implementos para asegurar su correcta conexión.
- Inspeccione el compartimento del operador y elimine cualquier residuo u obstrucción.
- Compruebe y ajuste los espejos.
- Familiarícese con el estilo de control y cámbielo si es necesario.
- Identifique los controles auxiliares/de enganche.
- Arranque el motor y revise los indicadores y advertencias de la consola.
- Si está equipado, compruebe la cámara de visión trasera.
- Revise todo el entorno externo desde la cabina.
CONCLUSIÓN
Una “comprobación en círculo” visual o una inspección preoperacional del equipo antes de cada uso reducirá la posibilidad de que el equipo funcione en condiciones inseguras. Esto facilita la detección y el tratamiento temprano de los problemas de mantenimiento antes de que se conviertan en un problema que provoque tiempos de inactividad, daños en los equipos o reparaciones costosas.