Warehouse Safety Meeting Kit
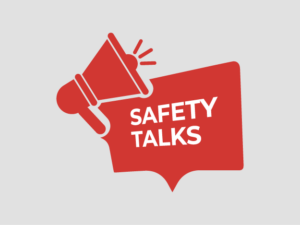
WHAT’S AT STAKE
Warehouse safety is a set of regulatory guidelines and industry best practices to help warehousing personnel ensure a safe work environment and reinforce safe behavior when working in warehouses.
Warehouses can be dangerous places to work in. It is important to understand common warehouse dangers and hazards because they can cause injuries and in extreme cases death.
WHAT’S THE DANGER
COMMON WAREHOUSE SAFETY HAZARDS.
Forklifts. Forklifts are critical pieces of equipment used in warehousing and storage facilities. However, when operated incorrectly can cause serious damage to operators, nearby workers and property.
Docks. One of the worst accidents a worker could suffer when working in a warehouse is being pinned or crushed between a forklift truck and the loading dock.
Conveyors. Conveyors pose serious dangers to workers including getting caught in equipment and being struck by falling objects.
IMPROPER/CARELESS SAFETY PRACTICES
Materials storage. Improper stacking of loads and storage of materials on shelves can result in unintended slip and trip hazards for nearby workers.
Manual lifting/handling. The most common cause of physical injuries in warehouse and storage facilities involves improper manual lifting and handling. Failure to follow proper procedures can cause musculoskeletal disorders, especially if done with awkward postures, repetitive motions, or overexertion.
HOW TO PROTECT YOURSELF
REQUIRED WAREHOUSE SAFETY PROGRAMS
To ensure the safety and security of all warehouse workers, the following programs/protocols must be established.
Hazardous Chemical. Hazard communication program should cover effective training on identifying chemical hazards; proper handling, storage, and disposal of chemicals; and the use of appropriate PPE (personal protective equipment). It is imperative that workers and management teams be knowledgeable in conducting better safety inspections and proper handling and storing of hazardous chemicals to ensure warehouse safety.
Energized equipment. A Lockout/Tagout (LOTO) program must be implemented in all warehouse operations to ensure that all energized equipment is properly shut off and to prevent employees from being caught between mechanical parts or being electrocuted. All affected workers must be trained on LOTO procedures and how to apply and remove LOTO devices after performing maintenance to ensure warehouse safety.
GUIDELINES TO KEEP WAREHOUSES SAFE
- Ensure Safety Equipment is Used at all Times. Forklifts or hydraulic dollies are used to lift items that are too heavy. Appropriate eyewear and hard hats should also be worn when required. Employees should be aware of emergency exits and the sprinklers installed in the roof should not be blocked at any time.
- Eliminate Any Potential Safety Hazards. Ensure all warehousing floors are free of ‘slip and trip’ hazards. It is important that this safety check is carried out on a regular basis, by all employees, and that the floor is always free of stray cords, liquids, and any other potentially hazardous items. It is also essential that any cracks and pits in the flooring are attended to as these can cause serious injuries to employees.
- Clearly Label Designated Hazardous Zones. Dangerous equipment should be stored away in an area that is clearly labeled and safe walk ways should be highlighted through necessary signage. The easiest way to illuminate hazardous zones is by using tape or painting black and white stripes on the floor of the designated area.
- Always Use Safe Lifting Techniques. When a load requires transporting, firstly assess what method is the best option for its movement. If lifting is the most suitable method; check the route to ensure no obstacles are in the way and ensure there is enough space for the load at its destination. Safe lifting techniques should always be carried out and the load should not obstruct the view of the lifter. Use all materials handling equipment carefully and follow the proper operating procedures including push rather than pull, whenever possible and lean in the direction that is being travelled. Never drive a forklift or use other powered equipment without training or authorization.
- Provide Training and Refresher Courses. Ensure all staff are educated and up to date with knowledge about safe practices within the workplace. most commonly occur when corners are cut in an attempt to save time.
- Promote Awareness in the Warehouse. Having a sense of awareness in the work place is an important safety factor. This can be achieved through communication between staff members. By employees being vocal and yelling out to others their location, collision incidents can be drastically reduced. All staff members should be encouraged to be constantly aware of what’s around them and to communicate where they are to ensure the avoidance of collision accidents.
- Ensure that all fire hazards are minimized and that appropriate fire safety measures are in place. An operating warehouse facility has all the necessary fire alarms, extinguishers, and sprinklers as required by safety regulations in your area. Schedule regular training and inspections to ensure that all employees are knowledgeable in fire safety processes and that all fire safety measures are in place and functioning as required.
- Minimize cutting dangers and enforce safe handling of sharp objects. Workers in a warehouse environment constantly use a lot of corrugated, metal, and plastic straps and plastic pallet wrappings. It’s vital that they use proper PPE and safety knives to avoid serious injury or death. Safety knives should retract automatically, limit the exposed cutting surface, and not require too much sharpening. All workers should also be trained in the proper cutting techniques to ensure warehouse safety at all times.
- PPE Required in a Warehouse. OSHA requires employers to provide all employees in a warehouse with the appropriate PPE (Personal Protective Equipment). Each employer is also responsible for:
- Providing needed PPE for employees
- Training employees on proper use and care of PPE
- Maintaining PPE and replacing as needed
The onus for proper PPE use doesn’t just fall on the employer. Employees must properly wear PPE, attend training sessions, care for, clean and properly store PPE and inform supervisors when PPE needs to be replaced or repaired.
FINAL WORD
Creating a safe and productive warehouse setting starts with a culture of safety. This culture should be reinforced by the managers at all levels, especially executives and owners.